Speed up your Additive Manufacturing simulation workflow
The fastest workflow on the market for design, preparation and simulation of the Additive Manufacturing process.
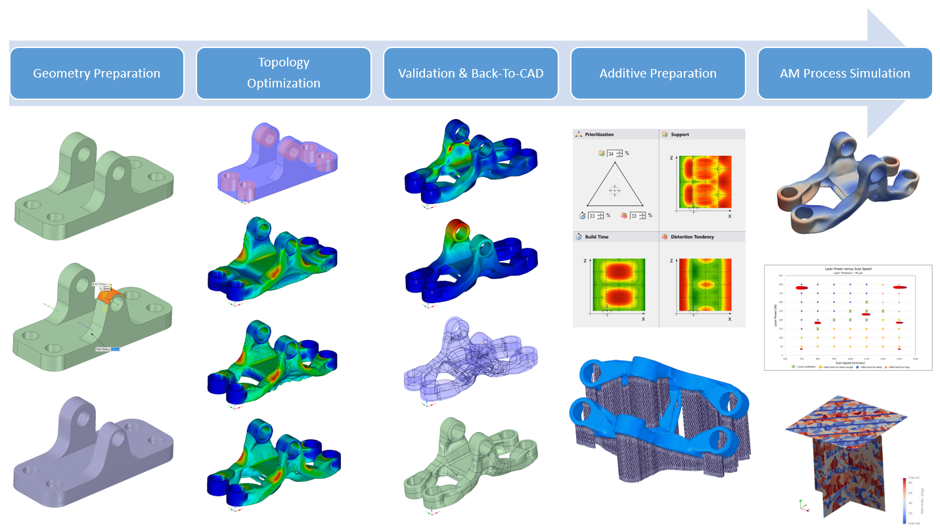
This workflow will bring your concept from just an idea to a 3D printable component in a process counting minutes rather than hours, or even days. A part of this process can be to perform topology optimization, where you are be able to investigate structural results live for every iteration step. This makes it possible to immediately validate your component or even do sensitivity analysis for changing load conditions.
From experience a tedious step is to clean up an optimized STL geometry and try to reproduce it in CAD format. Using the software an automatic tool can convert the STL geometry back to CAD within just a few minutes.
With an optimized geometry ready for 3D print, a natural next step is to search the optimal orientation on the build plate, for instance with an objective to minimize distortion tendency. This is done in an intuitive way and with the orientation set it is a simple task to automatically create a support structure, with several strategies to choose from.
To maximize successful builds and minimize waste of material, resources and time caused by trial and errors in an expensive printing machine, the process simulation will give valuable answers to how the part will behave. Typically, the risk for recoater arm collision and potential locations of crack initiation during the print process can be analysed.
To find out more about ANSYS software solutions and Additive Manufacturing (AM) process simulations.