FluentMesh just did my life much easier and happier.
Parallel option with Mosaic meshing.
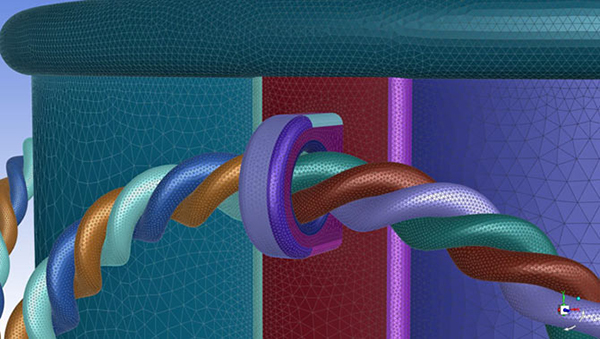
It helps me to set up the correct sizing’s, regions, inflation’s, etc. Another thing is how easy it is to start, especially if you have never used it before. With the new connection to SpaceClaim, you can launch FluentMesh from within SpaceClaim. You don’t need to bother about closing and opening software, save files in the correct formats – just one click and you are ready to go!
What really struck me with the latest release, is the parallel option with Mosaic meshing. There were multiple times, in the beginning, I thought the mesh had failed because it had stopped when I was looking at the session. However, when looking more carefully I realized, it was already done. A mesh I expected to take ~1 hour was done in ~20 minutes!
Read the top three tips to simulate fluid models.
Over the years, computational fluid dynamics (CFD) software has simplified the prepping and meshing of fluid models — making CFD technology more accessible to the general engineering community.
Here are three best practices for simulating fluid models.
Wrapping a mesh around geometry will simplify the setup of a fluid model.
The geometry that designers send to engineers is rarely clean enough to import into a fluids model. Fixing these gaps and leaks in the geometry can traditionally take hours, even days.
Therefore, engineers should use a CFD software that can wrap a surface mesh around is continuous geometry. This meshing capability will quickly fill in all the gaps, leaving more time for simulation and results generation.
For example, ANSYS Fluent’s fault-tolerant workflow for non-watertight geometries can create that surface mesh wrapper.
The flow volume is created by combining overlapping geometry into one surface.
Engineers can create a flow boundary by wrapping a box around watertight geometry and combining all the overlapping faces between the solids into one face.
This will resolve the intersections between the box and source geometry. The volume can then be extracted and imported into a fluids model.
Engineers can use the “share topology” function to create the flow geometry using ANSYS SpaceClaim. With Fluent’s “surface mesh” operation, they can extract the flow volume from the void between the boundaries in the geometry.
Engineers can reduce computational times by creating fluids models with coarse meshes for large areas and fine meshes near detailed geometry. The challenge then becomes linking these disparate meshes together without gaps.
Linking meshes is a tedious job. It typically requires cleaning up the geometry and manually correcting the meshes so everything fits nicely together.
A simulation using Mosaic-enabled meshing technology
ANSYS Fluent’s Mosaic-enabled meshing technology can automatically link these grids using a poly-hexcore mesh. Any type of mesh can be connected using this technology, including:
Tetrahedral meshes
Hexcore meshes
Polyhedral meshes
Poly-hexcore meshes