Exploring the Universe: Simulation Innovations for Space-Based Telescopes
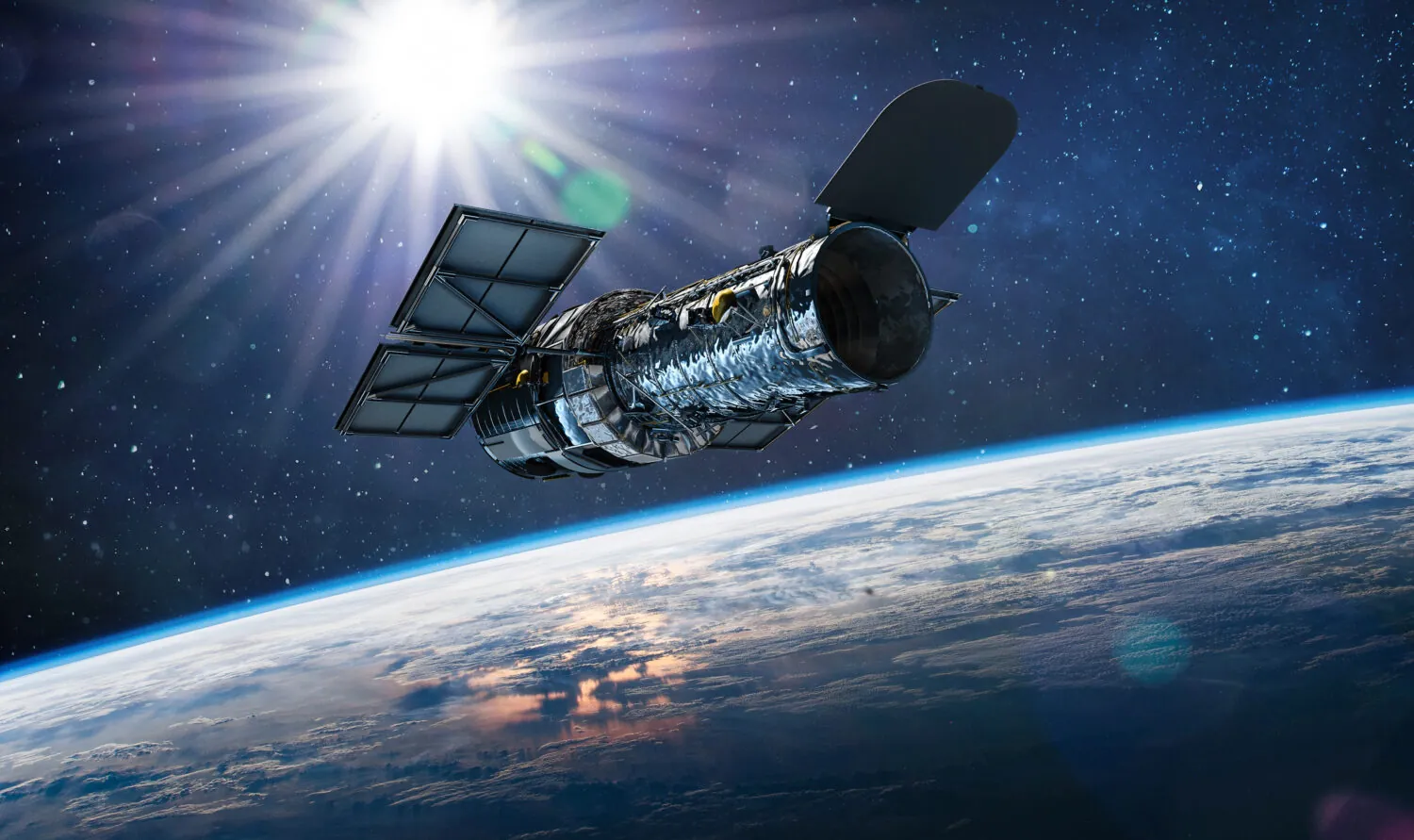
The vastness of space has long inspired humanity to explore its mysteries. Space-based telescopes, advanced tools of science and engineering, are essential for uncovering the secrets of the cosmos. However, designing these telescopes is a complex challenge, requiring every component to operate reliably in extreme conditions while meeting precise scientific demands.
Question: How do engineers tackle this challenge? Answer: System-level simulation! This revolutionary approach drives efficiency and precision in the development of Space telescopes.
Space telescopes are much more than scientific instruments; they are portals to the universe. Their role in expanding our understanding of the cosmos cannot be overstated. From capturing the faint glow of distant galaxies billions of light-years away to monitoring Earth’s weather systems with unprecedented accuracy, these instruments transform our ability to observe and understand the natural world.
Unlike their ground-based counterparts, space telescopes operate free from the distortions of the Earth’s atmosphere. This advantage allows them to observe the universe across a broader range of the electromagnetic spectrum, including infrared, ultraviolet, and X-rays. However, this bandwidth comes at a cost. The hostile environment of space presents critical challenges to the design and operation of these instruments, pushing that push the boundaries of engineering and materials science.
Building a telescope that can thrive in the vacuum of space is a complex and design sensitive process. Engineers must contend with a range of design challenges that are unique to this environment:
Each of these challenges represents a significant hurdle. Solving them requires a new way of thinking – one that embraces integration, simulation, and optimization at every step of the design process.
System-level simulation is game-changing in the design of Space-based telescopes. By integrating multidisciplinary engineering processes into a unified workflow, simulation tools enable engineers to model and optimize every aspect of a telescope’s design before it is built. This approach includes:
Detector development:
Optical and mechanical integration:
Thermal and structural analysis:
STOP Analysis:
By integrating these processes, system-level simulation reduces the need for physical prototypes, accelerates development timelines, and minimizes the risk of costly design errors.
The journey of creating a space telescope is one of iteration and refinement. System-level simulation tools provide engineers with a structured workflow, enabling them to address every aspect of the design process.
Stray light analysis:
Stray light, caused by unwanted reflections and scattering within the telescope, and unwanted coupling from external sources can degrade image quality. Simulation tools such as Zemax OpticStudio and SPEOS are used to identify and mitigate these pathways by modeling such stray light and the effects of sources such as sunlight and infrared self-emission.
Optical development:
Engineers optimize the design of lenses, mirrors, and other optical components to achieve the desired resolution and sensitivity. This involves simulating the telescope’s performance across a broad spectrum, from microwave to infrared wavelengths.
Thermal analysis:
Thermal simulations predict how the telescope’s components will respond to the extreme temperature variations in orbit. These simulations guide the selection of materials and design of thermal control systems to maintain stable operating temperatures.
Structural analysis:
Structural simulations model the mechanical stresses that the telescope will experience, from the vibrations of launch to the forces exerted by its own weight and movement in space.
System integration:
Once individual components are optimized, they are integrated into a single simulation to evaluate overall performance. This step ensures that all parts work together harmoniously, delivering the desired scientific results. Ansys software tools such as OptiSLang can assist in this process by automating the integration of different components, performing sensitivity analyses, and optimizing system-level performance.
A great example of system-level simulation in action is the design of Earth-imaging telescopes. These instruments must balance precision and durability, capturing high-resolution images of our planet while withstanding the challenges of low Earth orbit.
Engineers begin by simulating the telescope’s optical system, optimizing parameters such as wavefront error and the modulation transfer function (MTF) to achieve the required resolution.
Next, thermal and structural analyses ensure that the telescope remains stable under varying temperatures and mechanical stresses.
Finally, STOP analysis combines these results to account for real-world conditions such as thermal gradients and structural deformations, and ensuring the design performance is robust to environmental effects.
This process not only improves the performance of the telescope but also reduces development costs and timelines, making advanced Earth-imaging capabilities more accessible.
Cutting-edge software platforms, such as Ansys Mechanical, Zemax OpticStudio, and Speos, play a central role in this workflow. These tools enable engineers to:
For example, Zemax OpticStudio allows engineers to analyze light paths within the telescope, identifying potential sources of image degradation. Ansys Mechanical provides detailed insights into how structural deformations affect optical performance, enabling iterative refinement of the design. Speos provides system level optical simulation of the optical performance and advanced sensor design with a real time preview of the telescope in orbit.
As technology advances, the capabilities of space telescopes continue to grow. System-level simulation is the driving force behind this progress, enabling the design of telescopes that are more powerful, reliable, and cost-effective than ever before.
Looking ahead, these innovations hold the promise of unlocking new frontiers in space exploration. From mapping the surface of distant exoplanets to studying the origins of the universe itself, the next generation of space telescopes will push the boundaries of human knowledge.
The universe is vast, but with cutting-edge simulation technology, humanity can uncover its secrets with unprecedented clarity. Space-based telescopes, powered by robust simulation tools, are leading the charge in our quest to explore the stars.
Engineers and scientists are not just building telescopes—they’re ‘constructing bridges’ to the unknown. As technology evolves, who knows where the next generation of space telescopes will take us?
Find out more about Ansys Optics solutions
Find out more about our solutions for Space