Fast Tracking Next-Gen Electric Traction Motors with Ansys
Rail systems engineers have been tasked with creating an enhanced, high-powered electrical traction motor with torque density, which will help trains run more efficiently, consume less fuel, produce fewer emissions and reduce overall energy consumption.
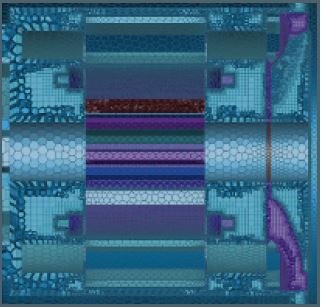