Fatigue life prediction: complementing structural analysis with particle simulation
Fatigue life prediction: complementing structural analysis with particle simulation
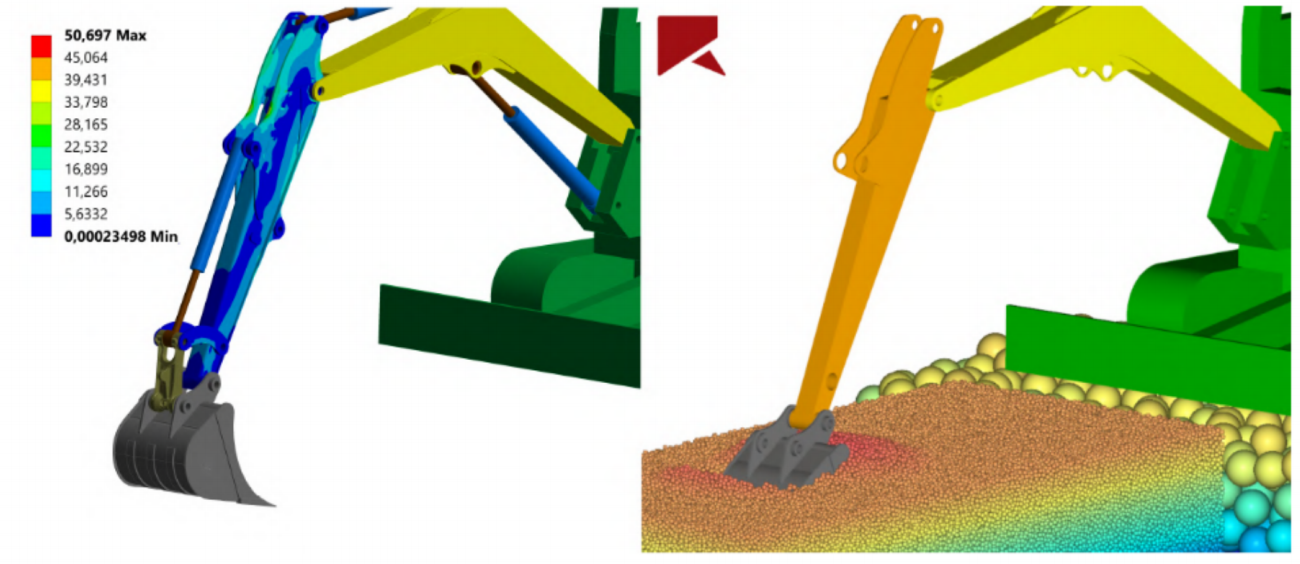
Chances are you know that a Bobcat machine. Despite its small size, is the “go-to” job-site workhorse. Its namesake company is a global leader in developing compact equipment that serves the construction, agriculture, landscaping, and grounds-maintenance industries. The Bobcat corporation, part of the Doosan Group, offers quality products that empower people to do more and has built its reputation on performance and dependability.
Bobcat products’ steel structures are especially important to ensure robustness and extend equipment life. Like many R&D teams around the world, Bobcat engineers apply mechanical FEA to predict how a part or machine system behaves under given conditions, which helps to identify weak spots and areas of tension. We’re interested in interpreting these simulation results not just as they relate to stresses from certain loads, but also how these repeated actions affect equipment life.
To better understand fatigue and equipment life, Bobcat developers combined DEM and FEA simulations to account for particle loading.
We leverage FEA tools to reliably predict and analyze the extreme conditions that a product encounters ─ and though these analyses are good for assessing mechanical properties, they are not proficient in the assessing the life of the product under different operating conditions. That is why we also perform fatigue analysis.
In addition, for our application the loading changes depending on our machine type and application including for example what type of material the customer is working with. We wanted to design a set of simulation capabilities that brings all pieces of this puzzle together, so we considered a scenario that included loading and used a compact excavator as a case study. Typically, excavators dig into the ground, coming into contact with different types of soils. Unlike the fatigue that road vehicles sustain, excavators’ most-damaging loads don’t come from extreme dynamics. Excavator fatigue generally comes from contact with the environment, specifically, what the excavator is digging. When broken down to its basics, dirt comprises individual particles that interact with each other as well as with the surfaces of the tools the particles come in contact with, exhibiting forces of repulsion, bonding, and friction. We expected that Rocky Discrete Element Modeling (DEM) tools would be highly useful for this study.
Particle action on excavator bucket under normal stress.
Instead, they planned to add different types of results to the mix, giving us another piece of the whole picture. We were not trying to build more precision on top of what we were already doing; instead, we were looking at the same thing from different points of view.
The study, that involved expertise from SVS FEM and resulted in a student’s proof-of-concept master thesis, created two computational models, one in Rocky DEM and a FEA investigation inside Ansys Mechanical. Discrete element modeling identified the effects of soil harvesting on the excavator’s components, with an outcome that included forces and moments of the excavator’s joints and the time that these occurred. The input parameters were found in literature (based on Bobcat’s intellectual property restrictions) that dealt with soil-ripper wear.
The physics of the bucket digging into dirt particles. When forces acting on the bucket’s outer side prevail, torque is negative (left); when forces acting are more prominent on the bucket’s inner side, torque is positive (right).
The DEM results would then be applied in Ansys Mechanical as an external load to the excavator’s joints, assessing elasticity and fatigue strength. The structural model used simplified geometry for the excavator arm and a more-detailed geometry model of the analyzed joint. All parts would be connected by rotational bonds, representing joints. Motion was defined by entering angular acceleration values into the joints. Simulation showed that the most significant results related to force and moment of the joint near the excavator bucket.
Coupled mechanical–DEM simulation represents excavator shaft stresses at any time during soil harvesting: von Mises stresses (left) and time instant (right).
Since this was a proof-of-concept, and not part of our usual development work, we did not know what to expect, especially since we wanted to compare the results with real-life Bobcat data. But the study results show that using Rocky DEM is a plausible solution to us, and it might deliver results in the range that we expect. We were able to set actual digging conditions and soil properties to determine how stress changes impact equipment life estimations. And by using Rocky, we became more convinced that we can achieve accurate results.
When interpreting results, we see that using DEM in conjunction with FEA can provide a very crucial understanding of what happens during excavation, for example. This is a powerful insight that will help us to understand equipment operational performance even better. We believe Rocky DEM will continue to provide value to our engineering and development efforts as we apply Rocky to more case studies and then validate and verify the results. We want to use simulation tools that reinforce our brand’s reputation for quality and performance. This is what the future of DEM holds for us.