From pet hair to barley
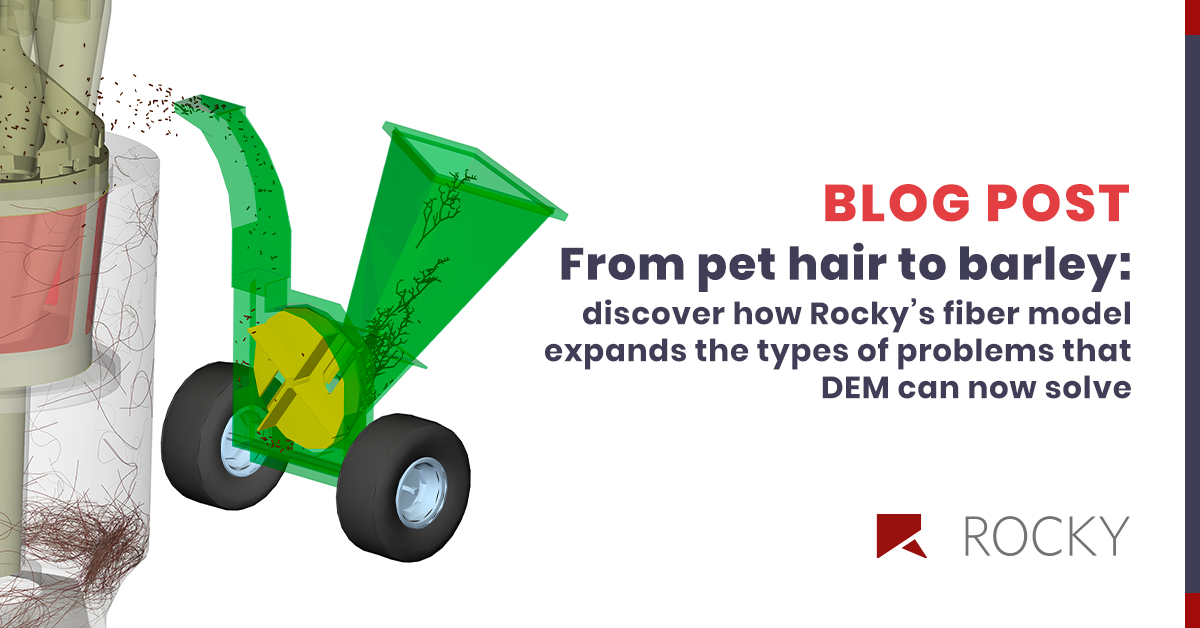
DEM has become a widely used design tool, and the types of materials that are modeled are more varied than ever. Real-world particles are quite often elongated, such as hay or hair, and particle flexibility needs to be accounted for when designing equipment to deal with such materials.
Traditional DEM codes model particles using a clustered- or “glued-” sphere approach. Although this method is easier to implement due to simple contact-detection algorithms for spheres, it does have significant disadvantages, such as the inability to efficiently model large-scale simulations containing such high-aspect ratio particles. For example, to accurately model an elongated hay particle with an aspect ratio of 1,000, at least 1,000 spheres (diameter 1 mm) need to be glued together, resulting in high memory requirements and long solution times.
Read this post for a better understanding of how the Rocky DEM fiber model overcomes these modeling challenges and allows you to efficiently model particles with large aspect ratios, such as hay, barley, pet hair, nets, logs, and more.
In Rocky DEM, the fiber shape category encompasses particles that are mainly one-dimensional, i.e., the geometry of a fiber can be described by a line (or several lines) in a three-dimensional space.
Fibers can be rigid, or if they are composed of multiple segments, flexible. In this approach, a flexible fiber is built by connecting sphero-cylinders by means of bonds with elastic and viscous properties, as depicted schematically in Figure 1.
Figure 1. Schematic representation of a flexible fiber.
For flexible fibers, when the adjacent elements move, the relative movement between them produces linear and angular deformations on the virtual bonds. In response, forces and moments are induced and exerted on the adjacent elements to resist the normal, tangential, bending, and torsional deformations.
The example below shows a fiber compression test simulated to acquire the force-deformation response curve and the hysteretic behavior of the hay. Both characteristics are then used to calibrate the hay material for future DEM simulations.
The fiber model allows you to model straight fibers (a linear shape, as shown in Figure 1) or create your own custom fiber shape by importing a .txt file. With custom fibers, sphero-cylinder segments can be arranged arbitrarily forming complex multi-branched geometries, as exemplified in Figure 2. The branches can have different diameters and nonuniform flexibility, enlarging the range of applications that can be modeled using DEM.