Electrification: How Simulation Powers Innovation in the Design of Components and Systems that Will Shape the Future
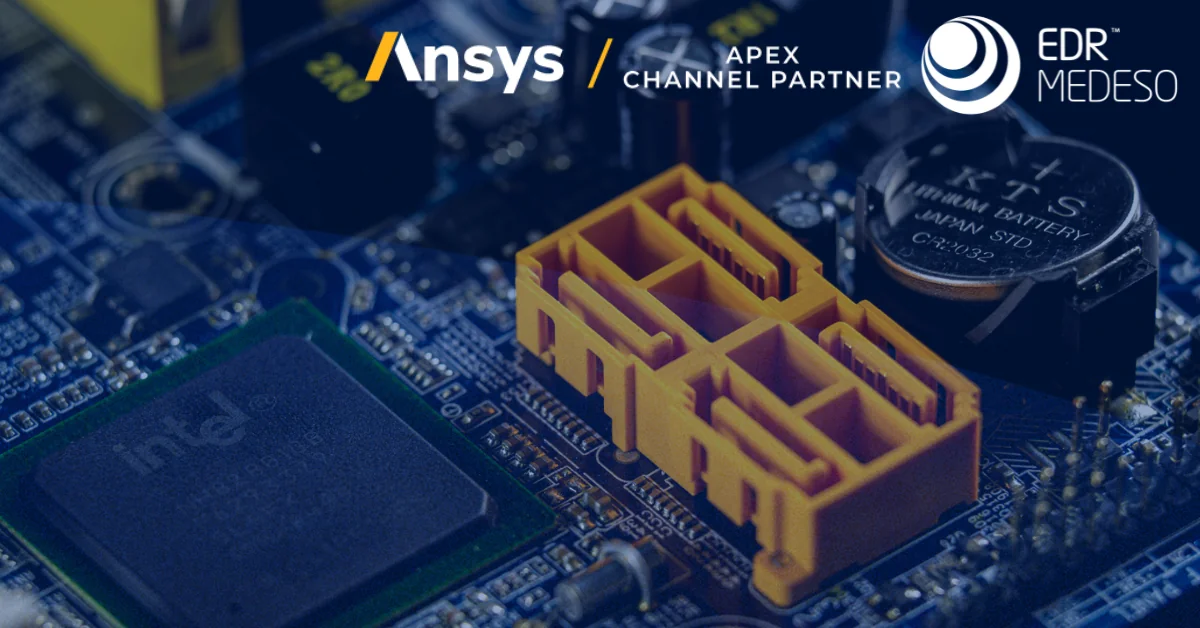
Electrification simply means going electric, or even more electric, as an environmental consideration in most cases. But that’s not all. Electrification can potentially provide improvements in reliability, flexibility, efficiency, and integration.
We rely on innovative solutions for an electric future, and simulation is one of the true enablers of innovation in the field of engineering design, helping engineers to design better products, faster.
Using simulation early, often, and throughout the design cycle can significantly accelerate product development, and lead to optimized products and systems. Moreover, it can pave the way for developing digital twins that will then be connected to physical assets, enabling optimized operation and predictive maintenance.
The key components of electrification include electrical machines (working as motors or generators), transformers (low or high frequency), power electronic inverters, cables and busbars, energy storage systems, actuators, and PCBs. As an example, think about electrified drivetrains in vehicles that include all these components. In such systems, integration and system-level interactions should be carefully studied to optimize their performance.
Simulation helps not only with designing high-performance components, but also with ensuring system-level efficiency and integrity, leading to something brilliant – holistic design and optimized performance of the system – instead of sub-optimization.
When it comes to simulation-powered design of the components, key areas of focus may be:
Here we use detailed high-fidelity models to accurately calculate quantities like electromagnetic losses, temperatures and stresses. In some cases, we may utilize multiphysics simulation workflows (either one-way or two-way couplings) to analyze the performance. For example, it may be needed to transfer losses/forces from electromagnetic models to thermal/structural solvers to calculate temperatures/vibrations.
High-fidelity component models are often large and slow, hence not very suitable for system-level simulations. The solution is ROM (Reduced Order Model) created from high fidelity simulations that can run fast while maintaining accuracy. For example, a widely used type of ROM in electrical engineering is an equivalent circuit including resistive, inductive, and capacitive parameters that can be calculated from high fidelity electromagnetic models.
ROMs can be created from models of different physics, and model reduction techniques may include both physics- and AI-based approaches. If needed, ROMs may be packaged as FMUs (Functional Mock-up Units) and used in any third-party software that supports FMI (Functional Mock-up Interface). This makes it possible to exchange the models between tools and companies, while ensuring intellectual property rights are protected.
Let’s have a look at two examples where ROMs can be used in simulation of electrified power trains:
Electrification is not just a buzzword. It’s a profound technological shift that is reshaping industries across the globe. And simulation is helping to develop innovative solutions that shape the future.
The leap to electrification is happening now – and those who deploy the power of simulation are better positioned to innovate and contribute to a more sustainable future.
This blog draws upon insights from Mostafa Valavi, PhD, presented at the Meet the Experts Simulation Seminar in Vejle, 2024.
If you’re looking to electrify your systems and accelerate your development cycle, contact us to learn more about how simulation can revolutionize your design process and help you build a more electrified future.