Industrializing Digital Twins in Windpower
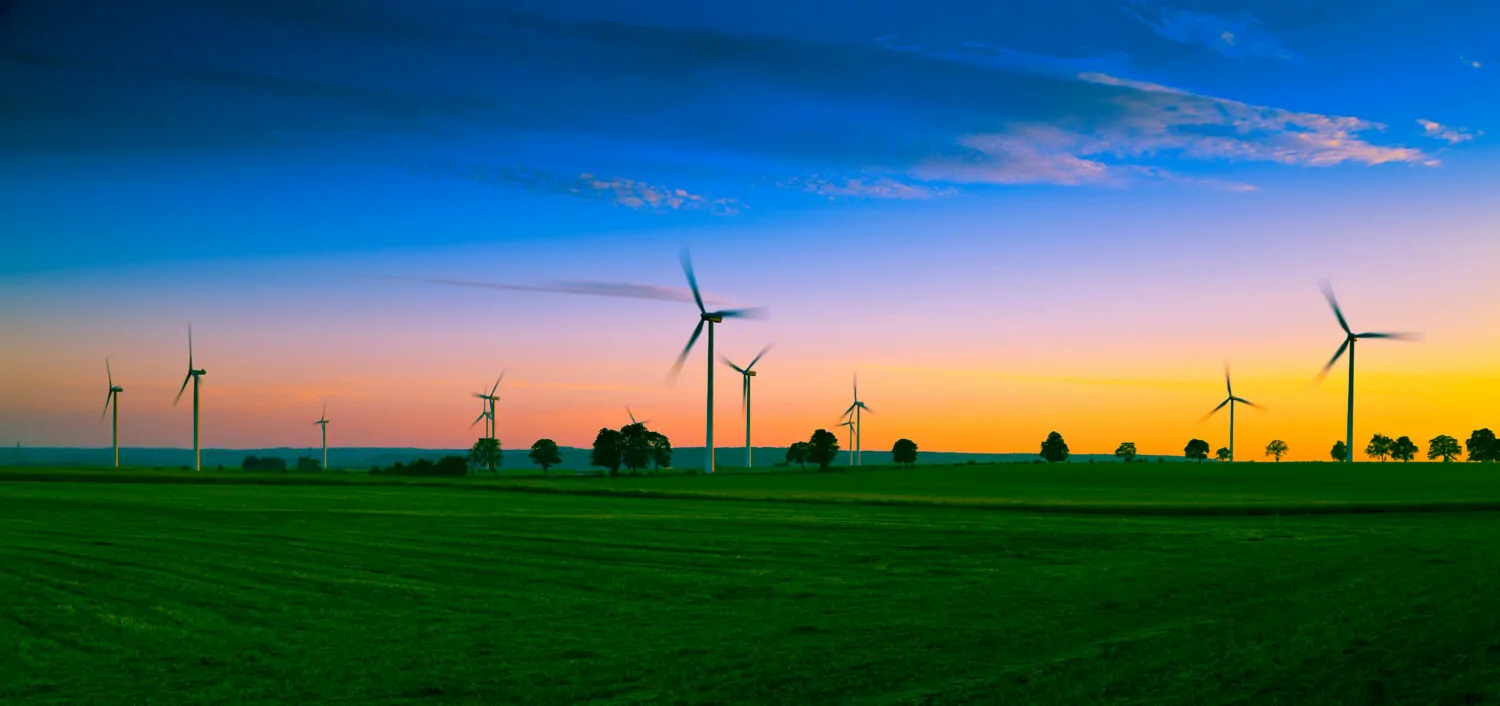
EDRMedeso is involved in several research projects with research/academic and industrial partners to develop the Digital Twin idea into practical and useful solutions that works in an industrial context.
With our several decades long experience in the Windpower industry it is natural for us to focus our Digital Twins efforts in this industry.
The wind industry is growing very fast worldwide, both onshore and offshore. However, the whole industry also experiences high failure rate of wind turbine components.
The ReliaWind research project, funded by the European Union, collected and analysed SCADA data measured on approximately 350 wind turbines in 2008-2011 and identified that wind turbine critical components as blades, main bearings and gearbox, were found to be the most vulnerable parts accounting for high failure rate and downtime. This is primarily because that the traditional operation and maintenance strategy is insufficient and it mainly adopts “passive” modes.
The goal is to employ digital and intelligent solutions for condition monitoring of wind turbine systems. Simulation and Digital Twin technology are key parts of this project – Mostafa Valavi, EDRMedeso
The goal is to use digital and intelligent solutions for structural health/condition monitoring to address the issues of high failure rate and high operation/maintenance cost of wind turbines.
To achieve this goal, a “perception-transmission-processing-utilization-control” digital solution will be proposed for operation and maintenance of wind turbine critical components. An advanced visualization platform, which supports data exchange and sharing among various parts, for wind turbine monitoring and fault diagnosis will also be developed and demonstrated.
Advanced technologies related to sensors, big data, deep learning and AI (artificial intelligence), are used to collect and process the multidimensional data on wind turbine critical components. Digital twin technology is used to combine monitoring data and simulation data for maintenance scheduling for the critical components.
Based on this, the early detection, diagnosis, traceability, prediction and visualization of faults as well as the remaining life prediction of wind turbine components can be realized. Additionally, use of the monitoring data can sufficiently improve the maintenance plans and therefore reduce the operational cost for wind turbines.
Project period: 3 years starting from Q3 2020