Particle Analysis and Cloud Computing Produce Mining Solutions Built to Last
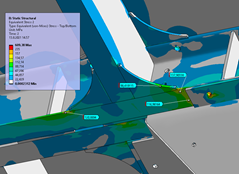
Whether their customer is a large quarry or a contracting business, Metso Outotec understands the daily equipment challenges that their customers face. Metso Outotec offers highly dependable equipment for the entire life of a business, leveraging extensive R&D and innovation skills in developing durable aggregate machinery.
Metso Outotec’s engineering team historically used Ansys structural simulation tools to optimize its hoppers, crushers, screeners, and conveyers. The one area that needed to be more accurately included in the simulation was how rock loads behaved as they were transferred into the equipment. Many mining machines are “black boxes:” The load goes in, the load comes out, but in between there is no way to visually monitor or measure what happens. Lacking a virtual tool, the team used engineering experience and reliable hand calculations, then produced prototypes that often needed to be performed multiple times. The solution lacked detailed engineering insight, and the final estimates precluded getting the design right the first time.
The Metso Outotec team decided to add Discrete Element Modeling (DEM) to their Ansys structural analysis simulations, and they selected Rocky DEM software. With Rocky simulations, Metso Outotec can include the transient behavior of particles and their loads on the equipment in a way that reflects real-world conditions─ validating the design and assuring customers that equipment will not fail in the field. Furthermore, Metso Outotec is using Rocky simulation to reduce and sometimes eliminate the need for lengthy and costly prototype testing.
Rocky DEM studies applied to real-life engineering problems can incorporate millions of particles, and DEM simulations, by nature, are transient calculations. To help accelerate the simulation run time, Rocky can run on multi-GPUs as well as high- performance computing (HPC) systems onsite or in the cloud. The engineering team at Metso Outotec decided to complement their in-house computing capabilities by running their simulations in the cloud at Rescale. Adding Rescale ─ a browser-based platform for managing and running high-performance computing (HPC) workloads in the cloud ─ has enabled more simulation.
For this feed hopper study, MO engineers needed to ensure that the structure would not fail when ~100-ton rock loads were applied. The structure was originally built in Ansys, and the same geometry was used in Rocky to predict particle behavior. DEM pressure load data was transferred to Ansys, identifying critical points in the beam joints underneath the hopper. Using the Rescale cloud platform, the solution converged in just a few hours.
and as much as two- to three-times faster calculation times than the computers available onsite. The ability to run Rocky on the local computers and on the cloud gave Metso Outotec engineering and IT teams the ability to decide how to best configure their hardware requirements and take advantage of Rescale computing power and cloud services.
As an example, engineers studied a feed hopper for structural-design limitations using Ansys software, Rocky DEM, and Rescale. The seamless combination sped up the entire process, reduced people-hours, and accurately identified how much loading the hopper could withstand and where the critical stress points were. The cloud system provided great cost savings and put the power of the latest NVIDIA GPUs to work for Metso Outotec engineers at a minimal, one-time cost.
Metso Outotec used Rocky DEM to investigate a dividing chute, identifying places where rocks impact with walls and create wear. The simulation results helped the engineering team to devise solutions that make equipment more dependable (such as adding panels that can be replaced when worn).
Today, many Metso Outotec products are designed by applying simulation prior to any prototypes being built and tested, a trend that is increasing. Adding discrete element modeling to structural analysis has improved the entire design process, since Rocky accurately predicts material flow. Rescale provides the ability to do more computational runs as well as complex analyses with millions of particles. The cloud solution provides ongoing benefits even as designers are added to the team or project deadlines get compressed. In the end, the company reaps the benefits of its engineering team spending more time applying simulation results to solve problems.
“Now that we know we can rely on our simulation results, Rocky DEM has improved our whole design process. We can do more runs, study more-complex problems, and get results faster. Before we added Rescale, we had to wait until our local hardware finished its run to start the next project. Now we have extra compute capacity when we need it. The combination of Rocky and Rescale gives us the confidence that the design is really valid, and we don’t need to rely on prototype build and tests as much as before.”
– Wiljami Nurmela, Engineering Manager, FEA & Simulations, MetsoOutotec
Metso Outotec needed to verify that its rock hopper’s structure could withstand the huge loads that mining customers pour into it ─ as much as 100 tons at a time, repeatedly. The company’s reputation as a frontrunner in sustainable mineral processing equipment was at stake. The build/test prototype process involved manually estimating and roughly scoping the loads, which produced less-than-optimum results.
The engineering team turned to EDR Medeso, an engineering solution provider that suggested adding discrete element modeling (DEM) to Metso Outotec’s simulation software toolkit along with a cloud computing solution to speed up solve time. Rocky DEM was the right fit for particle flow analysis, delivering accurate results and compatibility with Metso Outotec’s existing Ansys structural software. The Rescale platform added the ability to manage computation complexity, significantly speed up solve time, and tackle its most-challenging problems.
The combination of Rocky and Rescale has expanded Metso Outotec’s ability to offer dependable mining/aggregate equipment to its customers. Rocky DEM gives engineers the capability to look inside “black boxes” to study how particles impact walls and contribute to load stresses. Rescale’s platform enables engineers to run their most demanding software on the world’s largest cloud network, with no disruption to operations.