Pioneering Simulation at Grundfos: on Innovation, Leadership, and the Future of Engineering
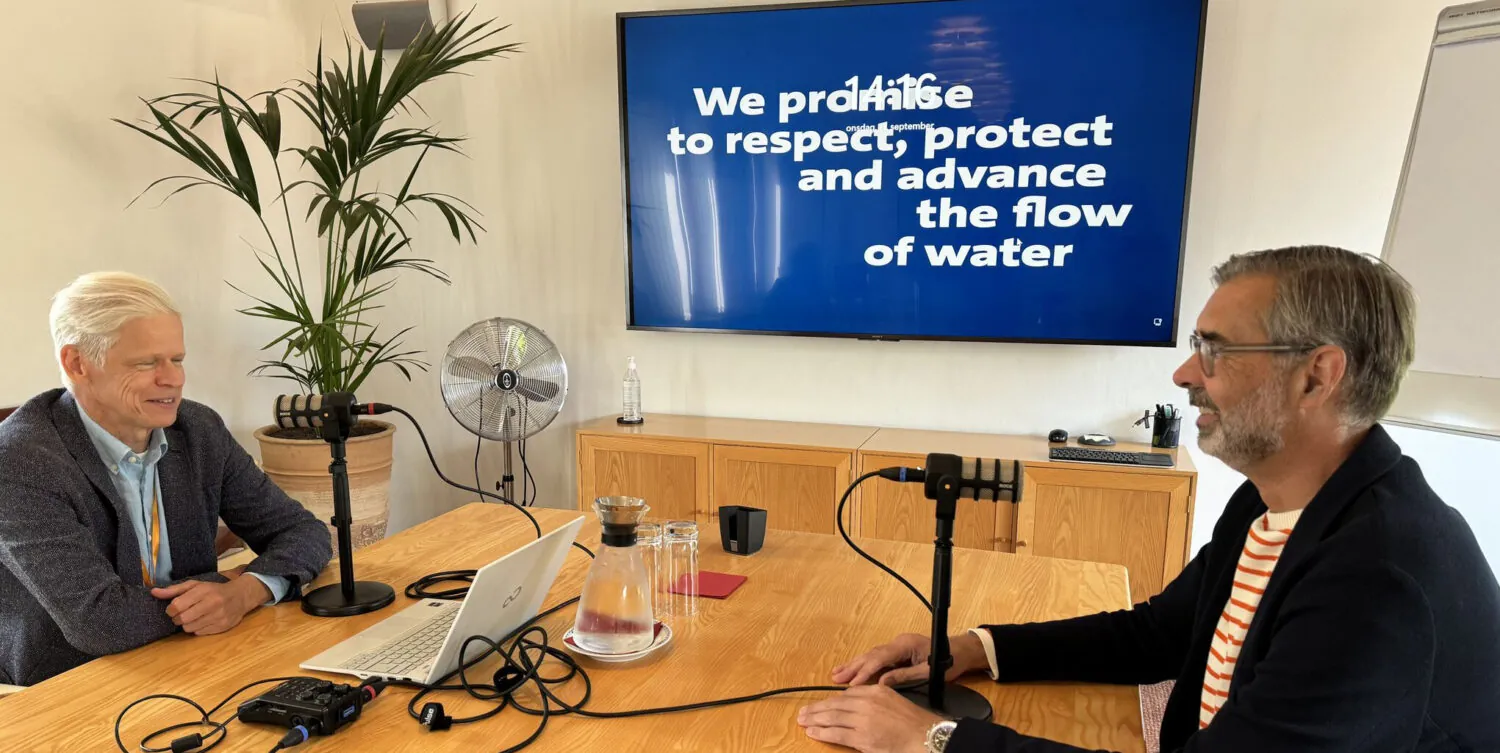
Christian began his career at Grundfos shortly after completing his PhD in swirling flow simulations. His background in simulation positioned him to lead Grundfos into a future where simulation became an integral part of the company’s design and development processes. Early on, Grundfos was already experimenting with using computers for engineering calculations—a pioneering effort led by its CEO at the time, Niels Due Jensen. With an engineer’s curiosity, Jensen quickly adopted new methods to enhance the company’s product development, and simulation was at the core of these innovations.
For Christian, the initial challenge was to embed simulation more deeply into various disciplines within Grundfos, from pump design to mechanical engineering. The real turning point came in 2013, when Christian and his team recognized the need for a cohesive strategy to incorporate simulation across the company’s development processes. This led to a collaboration with consultants to shape a simulation strategy that would ultimately transform how Grundfos approached engineering challenges.
One of the most significant insights from this journey was the realization that simulation could be used for more than just validation. Initially, Grundfos used simulation primarily to validate designs after they had been built and tested in a workshop. This approach was common in mechanical engineering, where products were designed, built, and tested in a repetitive cycle until the desired outcome was achieved.
However, the pump division had been using simulation differently – driving the design process from the outset, optimizing and refining the product before a physical prototype was ever built. This approach allowed them to complete thousands of design iterations in simulation, drastically reducing the need for physical prototypes and the time required for testing. Christian and his team saw the potential to apply this design-driven simulation model across all areas of the company.
To make this transition, Grundfos needed more than just new technology. It required a shift in mindset and a deliberate change management strategy. Christian described how they built a “burning platform” to create urgency around the adoption of simulation in mechanical design. The key to success was linking simulation to tangible benefits: faster development times, better product quality, and significant cost savings.
One of the pivotal moments in this transformation was realizing that to convince upper management, they needed to talk numbers. Engineers may understand the technical advantages of simulation, but executives often need to see the financial benefits. Christian recalled how data from literature showed that simulation could save up to 35% in prototype costs and 15% in development time. These numbers became a ‘guiding star’ for the team as they made the case for increased investment in simulation technology. One memorable moment involved a specific project where Christian was asked if they could save 16 weeks by using simulation. When he confidently answered yes and presented the cost savings, it marked a turning point. From that moment on, simulation was no longer just a technical tool—it became a strategic asset for driving innovation and competitiveness.
As Grundfos continued to see the benefits of simulation in product design, they began to explore other areas where simulation could add value. One of the most exciting developments was the use of simulation in production equipment. By simulating how production lines would operate, Grundfos was able to optimize its manufacturing processes, leading to further efficiency gains.
Today, Grundfos uses simulation throughout the entire development pipeline, from design exploration and verification to manufacturing. They have even started to use simulation as a sales tool. For example, when selling wastewater treatment equipment, simulations are used to show customers how the pumps or mixers will perform in real-world conditions. This not only helps close deals but also gives customers confidence in the product’s performance.
Looking to the future, Christian is particularly excited about the integration of simulation with artificial intelligence (AI) and the Internet of Things (IoT). As more devices become connected, the ability to harvest real-world data from products in the field opens up new possibilities for optimization and innovation.
However, real-world data is often incomplete or noisy, which is where simulation comes in. By combining real data with synthetic data generated through simulation, companies can gain deeper insights into product performance.
This is particularly relevant as AI and machine learning algorithms begin to play a larger role in analyzing and optimizing product designs. Simulations can help validate AI algorithms by providing a baseline of “correct” behavior against which the AI’s predictions can be compared. This blend of real and simulated data will become increasingly important as companies seek to leverage the full potential of AI in product development.
Despite the clear benefits, Christian acknowledges that widespread adoption of simulation has been slower than expected, particularly in small to medium-sized enterprises (SMEs). Many companies still see simulation as a tool for validation rather than design, or they use it only for troubleshooting when something goes wrong. Christian believes that part of the problem is the lack of democratization of simulation tools. While Grundfos has made strides in building tools that allow engineers to run simulations at the click of a button, there is still a need for highly specialized teams to drive the process.
The goal, however, remains clear: to make simulation accessible to a broader range of engineers and disciplines. Christian emphasizes the importance of change management in this process, ensuring that everyone in the company – not just engineers – sees the value of simulation. This includes using simulations in areas like sales and marketing, where visualizing product performance can have a significant impact.
Christian’s reflections on the past decade highlight the transformative power of simulation in driving innovation and efficiency at Grundfos. From reducing development times to improving product quality, simulation has become an essential tool for staying competitive in a rapidly changing market.
Looking ahead, Christian is optimistic about the future of simulation, particularly as new technologies like AI and IoT become more integrated into the development process. While there are still challenges to overcome, particularly in making simulation more accessible to SMEs, the potential for further innovation is immense. As more companies embrace simulation as a strategic asset, the pace of innovation is set to accelerate, bringing with it new opportunities for those who are willing to lead the way.
Listen to Christian in conversation on the Simulation Leadership Podcast