Revolutionizing Medical Device Development with Simulation: An Overview
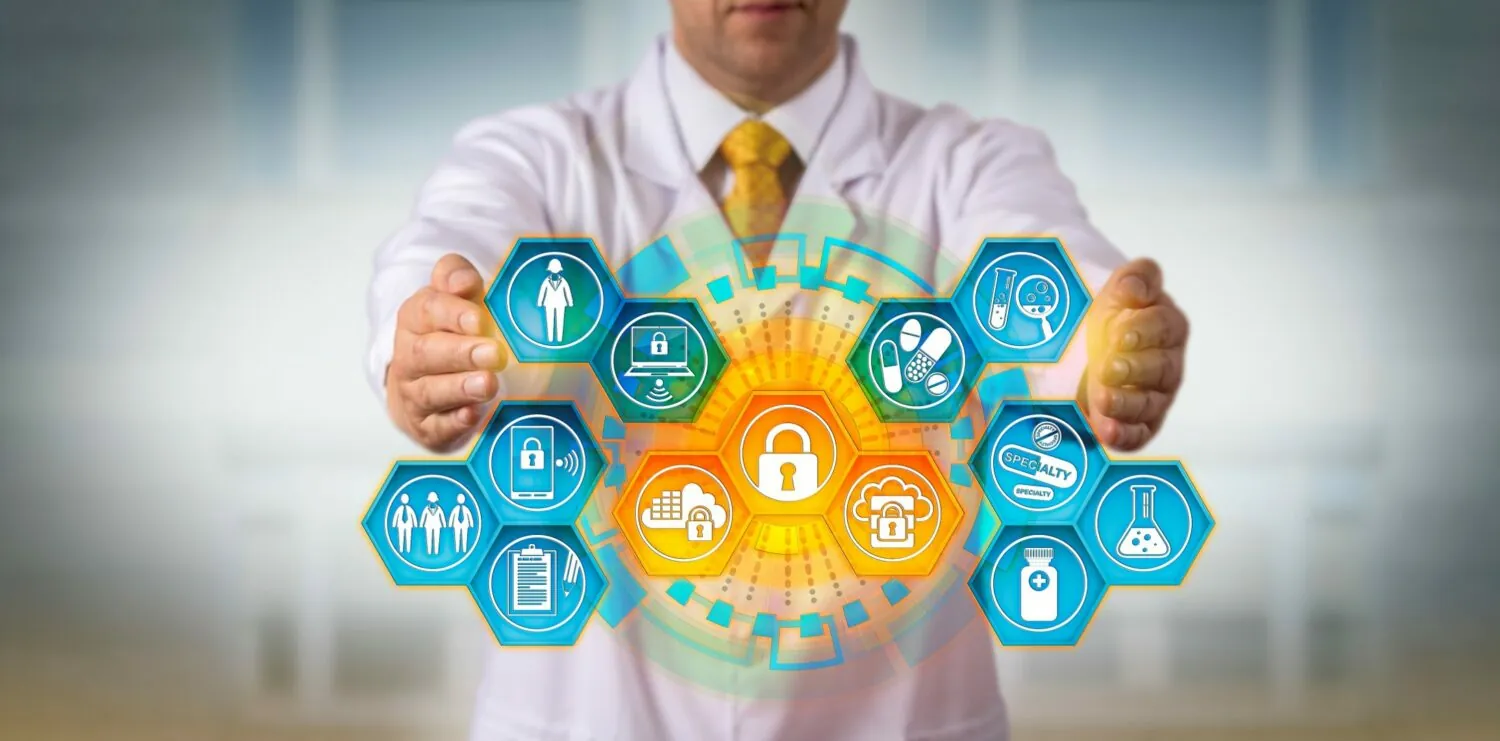
Watch the webinar on demand NOW!
Ansys is spearheading the in-silico medicine revolution by collaborating with policymakers, regional regulators, industry leaders, consortia like the Avicenna Alliance, and leading academics. Such efforts are making a significant impact, exemplified by a North American medical device manufacturer who used Ansys’ physics-based simulation solutions to shorten their time to approval and product launch by two years, saving $10 million in regulatory submission costs.
Healthcare companies rely on the accuracy of Ansys’ comprehensive simulation portfolio because of the work undertaken with both regulators and industry standards organizations to develop best practices. These models facilitate adoption and accelerate the regulatory approval process, ensuring that products are safe and effective.
Patient Safety: Ensuring extreme reliability of products is paramount. This is strongly linked to patient safety, which can be established by demonstrating compliance with industry standards and using materials that meet local policies.
Accelerated Development and Approval: Modeling and simulation not only speed up product development but also reduce the time required to generate safety evidence for regulatory approval, thereby reducing the need for extensive clinical trials.
Cost Reduction: By minimizing clinical trials and bench tests through rapid prototyping and simulation, companies can significantly reduce costs.
Increased Accuracy: as an example, using computational fluid dynamics and patient-specific lung geometries can increase the accuracy of drug targeting in the lungs by up to 90%.
Time Savings: incorporating modeling and simulation into the development cycle can reduce the typical testing time for devices like hearing aids by months.
Cost Savings: a $10 million cost reduction was achieved by minimizing the size of a clinical trial through effective use of modeling and simulation.
The total product lifecycle of a medical device includes invention, prototyping, evaluation in animals and humans, regulatory review, approval, and post-market monitoring.
Traditionally, computational modeling was limited to the design phase. However, the scope has expanded to include regulatory review, especially after the US FDA recognized computational modeling and simulation as credible sources of evidence for device approval.
This has paved the way for in silico trials, which use reliable computer models to reduce or replace clinical trials.
Stents Using finite element analysis (FEA) in Ansys Mechanical and LS-DYNA, various aspects of stent design, including deployment and fatigue life, can be modeled to ensure reliability.
Blood Pumps Computational fluid dynamics (CFD) is used to assess pressure-flow performance and biocompatibility, addressing concerns like haemolysis and thrombosis.
Blood pump example
Dry Powder Inhalers CFD and particle tracking help design inhalers that deliver drugs effectively to the lungs, minimizing waste and ensuring efficient drug delivery.
Metal Implants By combining HFSS and Mechanical, Ansys can model and predict the temperature rise in tissues near metal implants during MRI scans, improving safety without extensive bench testing.
Spinal Implants FEA and patient-specific models allow for the optimization of spinal implants, ensuring compatibility with additive manufacturing and compliance with industry standards like ASTM F2077.
Ansys collaborates with key policymakers and regulatory agencies, including the US FDA, and participates in the development of key standards. Through public-private partnerships and non-profit industry associations, Ansys is at the forefront of developing and sharing best practices for using simulation in regulatory filings.
Materials information is fundamental to the performance and viability of medical devices. Effective management of this information is business-critical, impacting design decisions, manufacturing operations, regulatory compliance, and purchasing. Ansys Granta MI serves as a certified source of materials information, helping organizations manage this data systematically and reduce risks, costs, and missed opportunities.
Ansys is revolutionizing the medical device industry by leveraging simulation technology to improve safety, accelerate development, and reduce costs. Through collaborations with regulatory bodies and industry leaders, Ansys ensures that simulation becomes an integral part of the medical device lifecycle, from design to regulatory approval. Embracing these advanced simulation tools can help healthcare companies lead in innovation and efficiency, ultimately benefiting patients worldwide.
Watch ‘An Overview of Modelling and Simulation in Healthcare’ webinar on-demand
Find out more about simulation solutions for the healthcare sector