Simulation best practices for additive manufacturing
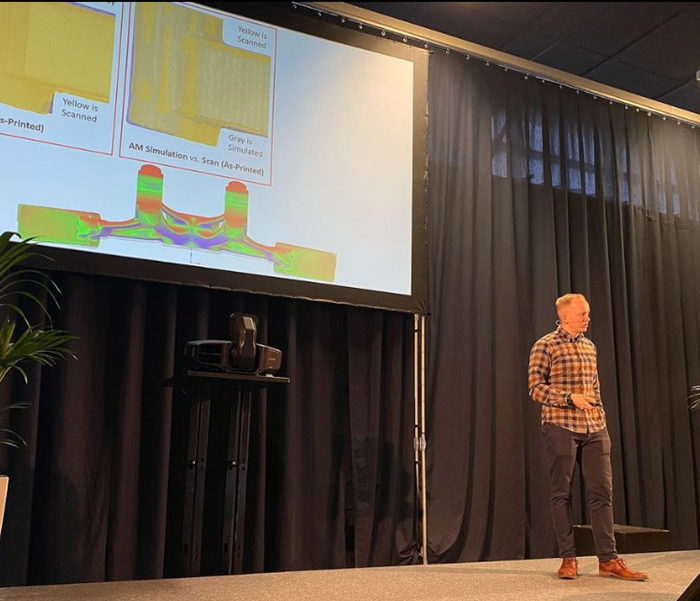
In spite of this, and all too often, the typical result of AM leads to waste and flawed products that have been printed incorrectly.
Why? Because the printed parts are often not what was expected, with errors occurring for many reasons. One typical example of this is when a product is optimized for weight, but thin material warps during the printing process due to, for example, heat. The material can also crack when it cools. It’s all too easy to continue making these mistakes due to the iterative print process, where many prototypes are made. One way to avoid this is to test the performance of the material in the printing process by carrying out simulation prior to printing.
Using simulation software from Ansys, the world’s largest provider of the most comprehensive solutions for AM, takes the guess work out of the process, and gives an insight into phenomena, like in the example mentioned above.
Picture: *Reducing Satellite Antenna Components from 100 Parts to 1
Printing metal is expensive. Printing a single metal part costs between 5 to 20K €, maybe even more. Mistakes are even more expensive. In addition to saving material costs, by carrying out simulation companies can save a huge amount of time, since one print can take up to three weeks to complete.
As shown by the example above, the cost of AM can be typically reduced by up to 75% – this is achieved by fewer failed prints and time that’s saved through not having to reprint.
1. Design
· Lightweighted, optimized geometry with similar or better performance
· Optimized geometry with minimum support requirements
· Comparative data for performance of initial part/assembly vs DfAM part/consolidated assembly for one or more physics
2. Build Setup
· Minimize distortion tendency, build time and/or supports through optimal orientation
· Customize build envelope dimensions
· Select individual regions to create supports of different types
· Generate build files
3. Process Simulation
· Prediction of distortion and residual stresses
· Detection of potential blade crash
· Distortion compensated geometries
· Baseplate distortion prediction considering multiple parts
· Consideration of the influence of heat treatments and cutoff direction
4. Material Analysis
· Meltpool and porosity prediction based on machine parameters
· Thermal sensor simulation — heat color map for a cross section of the printed part
· Microstructure predictions — grain size and orientation
5. Data Capture and Management
· Single source of materials information across whole organization
· Structured digital database with established links between various processes
6. Validation and Part Qualification
· Deviation from normal geometry
· Data for temperatures and porosity as a function of deposition speed and power
· Comparative stress and distortion plots
It’s impossible to make intelligent investment within an organization unless there is an understanding and acceptance that the entire industry is evolving. Already in an advanced stage of change, those who aren’t becoming more reliant on simulation in their product development processes, are lagging behind in this evolution. Using simulation as part of company strategy in the printing process helps to meet both increasingly pressured budget and time requirements. Further, achieving sustainability targets becomes easier when materials are saved by reducing the number of printings and thus reducing waste.
In conclusion, simulation integrated into the process prior to printing ultimately saves not only money, components and wastage, but also a huge amount of time. EDRMedeso is the only Ansys Elite Channel Partner in the Nordics and UK, why not begin your simulation journey with us and take your innovative solutions to the next level?
Metal industry trade fair Konepaja and the largest welding trade fair in the Nordics, Nordic Welding Expo, returned to the calendar after a four-year wait. The combined event was complemented by 3D & New Materials. The trio gathered 6,270 visitors in the halls of the Tampere Exhibition and Sports Centre from 28th November to 1st December 2022. EDR&Medeso was proud to take part as an exhibitor (Exhibition Booth B104), whilst Juuso Nänimäinen from our Innovation Team gave a presentation at the 3D Stage on the topic ‘Simulation best practices for additive manufacturing’.
Picture: Kimmo Korpela and Lauri Pisilä in our EDRMedeso stand
Picture: Juuso Nänimäinen, EDRMedeso