Space Forge Embarks on In-Orbit Manufacturing
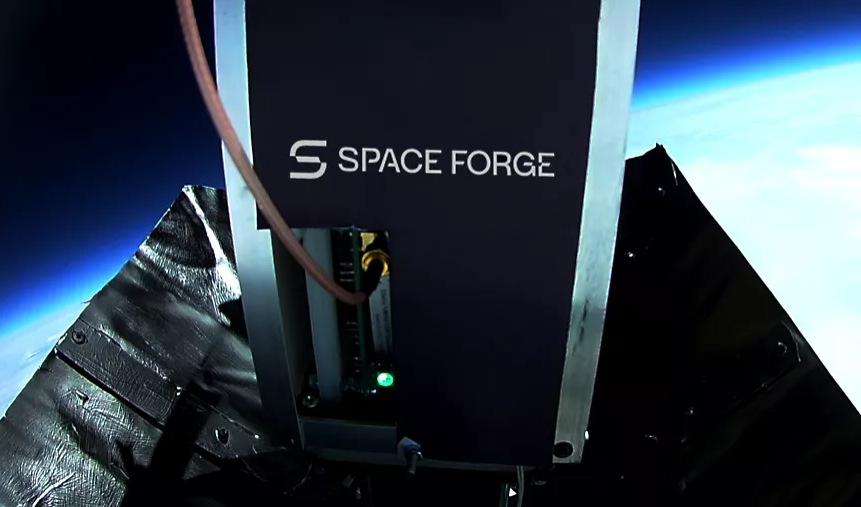
Imagine building a product from scratch without gravity, buoyancy, or other earthly hinderances. Think about constructing the most sensitive inner workings of a superconducting device without worry of contamination. Dream of manufacturing in an environment where nothing can compromise the integrity of your product.
These suggestions may seem a bit out there — because they are. In fact, they start about 500 kilometers — or roughly 300 miles — above the Earth’s surface in the beginning of the exosphere where astronauts aren’t the only visionaries turning far-out fantasies into realities.
Engineers at Space Forge, a manufacturing company based in the United Kingdom, are sending robots into orbit to assemble ordinary material in extraordinary ways on returnable satellites.
Early concepts for Space Forge began in 2018 when Andrew Bacon, an aerospace engineer, and Joshua Western, a satellite sales executive, recognized the potential of in-orbit manufacturing followed by return to Earth. But they knew they would need to create safer and lower-cost reentry technology to make it happen.
With an official company launch slated for March 2020 and having just quit their day jobs, it was less than ideal when the coronavirus pandemic sent most of the world into lockdown.
Still, as its name suggests, Space Forge was prepared to forge ahead. The dynamic duo used the time in isolation — largely spent connecting virtually from a garage — to strategize business plans and get things off the ground, literally.
Space Forge became a member of the Ansys Startup Program in early 2021 via Ansys’ UK Elite Channel Partner, EDRMedeso. The program encourages early-stage startups by offering affordable access to Ansys’ simulation solutions, including technical support for additional assistance.
Cofounders Joshua Western (left) and Andrew Bacon (right) speaking at the Space Forge grand opening.
By April 2021, Bacon and Western secured their first office space in Cardiff, Wales ready to grow their business and team. Today, Space Forge has more than 30 employees and expects to reach 45 by the end of the year.
The driving force behind Space Forge is its innovative ForgeStar Platform, which operates a fleet of returnable satellites. One of Space Forge’s most distinct offerings is that everything they send up comes back down, while similar launch vehicles tend to leave material behind to burn up in space.
In contrast, Space Forge ensures that your finished products, as well as your unused material, will return to Earth during a safe reentry and landing. The returnable satellites are uncrewed.
The main reasons for the human-free satellites are safety and cleanliness. To remove potential contamination, all products are manufactured by robots. Additionally, Space Forge adheres to all regulations from the Civil Aviation Authority, which monitors aviation safety in the UK and determines policy for the use of airspace, including which materials are allowed to make the trip.
With cleanliness and safety in place, Space Forge can embrace the other core benefits of manufacturing in space, including microgravity, ultra-high vacuum pressure, and near-absolute-zero temperatures — a trio of benefits that Bacon calls the “triple advantage of space.”
For example, quantum devices such as optical sensors, are incredibly delicate mechanisms that greatly benefit from cryogenic conditions. As Wien’s displacement law states: An increase in temperature causes a decrease in wavelengths at which the peak amount of energy is radiated. This can disturb the sensor’s precision, so low temperatures are optimal and near-absolute-zero temperatures are ideal.
Other instruments that benefit from space conditions include medical implant sensors that detect heartbeats and ultrasensitive compasses that let you know exactly where you are in the world instead of just indicating the direction of north.
In materials manufacturing, superalloys benefit from space, too. Gravity and buoyancy go hand in hand. Unfortunately, here on Earth, buoyancy prevents perfect alloying in metals of different densities. In microgravity conditions, buoyancy is eliminated.
So, how does space manufacturing work for a huge piece of equipment? Well, it gets down to the nuts and bolts of it.
Let’s look at a wind turbine blade. Sending entire blades to space one by one to manufacture could be quite cumbersome. However, the bolts that connect the parts of the blade actually undergo the most stress and are much smaller and easier to ship to space. By perfecting the bolts, you can increase the size of the blade.
Likewise, for aircraft turbine blades, the superalloys that fasten the blade to the engine are equally important to the overall endurance of the blade.
The same “less-is-more” concept is true for semiconductors in mobile connectivity. While it would be to expensive and time-consuming to ship up the semiconductors of every single cell phone, it’s not as extensive to consider a selection of semiconductors that are used in cell phone towers. In most instances, you don’t need a lot of product or material to make a significant impact.
Of course, Space Forge envisions large-scale production in the future, but for now remains focused on the smaller steps with the most advancement.
Trip time varies depending on the project, which is an uncommon luxury. The International Space Station, for example, typically requires years to get experiments to and from space. But through the ForgeStar Platform, trips can range anywhere from two weeks to six months. Biological research or pharmaceutical manufacturing typically require shorter trips, whereas semiconductor manufacturing or projects that involve vaccine research take longer periods of time.
As Bacon explains it, Space Forge is all about embracing the trifecta of ideal conditions in space to create the “perfect manufacturing environment” while enabling lower-cost return flights, which are made possible using the predictive accuracy of Ansys software.
One of the most important factors in designing a reentry vehicle, or returnable satellite, is accounting for the contrasting levels of speed and altitude within a short amount of time to maintain stability.
Within an hour your vehicle drops from an altitude of approximately 400 kilometers, or about 250 miles, at a speed of Mach 25 — more than 19,000 miles per hour — to sea level at around 20 miles an hour.
“You’re transitioning through a whole range of different speeds and altitudes and it’s really important that your vehicle is stable,” Bacons says. “We looked at which software could model anything from sea level up to hypersonic speeds and Ansys won that trade-off with its computational fluid dynamics (CFD) and Ansys Fluent in terms of what range it can simulate and what kind of geometry it can handle.”
Combined with the engineering confidence that Ansys simulation supplies, Bacon and his team embrace additional benefits of the Ansys Startup Program, including cost-efficiency and technical assistance, which Space Forge received from Sheffield-based Ansys experts, EDRMedeso.
A close-up of return technology at Space Forge
“There are other packages out there, but their support is not great,” Bacon adds. “We knew we were going to be doing something quite advanced, so support is really necessary. Comprehensive knowledge coupled with the ability of the EDRMedeso technical team to embrace our particular approach to simulation have been key factors to our success. And the Ansys Startup Program pricing is pretty fantastic along with the fact you get access to all the other modules as well.”
Naturally, reentry was the first challenge Space Forge explored and validated using Ansys’ simulation.
To test the satellite’s return, the team built a simplified, cone-shaped version of the satellite and modeled it in Ansys Fluent to analyze its dynamic stability, particularly when spun around as if caught in a gust of wind. The team took the cone to Pembrey West Wales Airport and dropped it from a drone about 400 feet overhead. While it worked the first few times, as the wind intensified the cone flipped over and rolled out of control. In review of their simulation results, the team confirmed that although the center of mass was in the correct location in the simulation and demonstrated dynamic stability, they didn’t implement the additional values when setting the center of mass for the actual drop test.
Out of curiosity, they ran the simulations again, inputting the incorrect center of mass from the failed attempt, and the simulation showed the cone spinning out of control.
At that moment, the team knew they had verifiable, trustworthy solutions and wouldn’t again stray from the simulation data or “cut corners” as Bacon says.
“Satellite reentry is probably one of the hardest problems you can try to do in space, and to do it you need the best software,” says Bacon. “The vast majority of software we just didn’t even consider because it couldn’t do the job, but our experience with Ansys is that it’s doing the job, and certainly a lot of the software out there couldn’t have.”
To improve satellite reentry further, Space Forge engineers developed Aether, a predictive analytic tool that they use in conjunction with Fluent to better determine reentry landing locations.
Engineers analyze the static and dynamic stability of the satellite using Fluent and consider varying regions throughout its flight, including a range of speed from Mach 25 down to Mach 0. After collecting an aerodynamic database of coefficients, the team inputs the data into the Aether to calculate landing locations, while applying the direction and speed of wind as input values for potential drag.
As a bonus, Space Forge can automate their calculations and simulations within the software, which streamlines the team’s workflow and allows for more consistency and longer run times. Automation is particularly helpful as many of the team’s simulations run for weeks at a time.
Another advantage and selling point for Bacon and his team was the ability to implement Ansys’ simulation on Amazon Web Services’ (AWS) cloud platform to run simulations with even more computing power — a capability made possible through a longstanding relationship between Ansys and AWS.
In addition to CFD, the Space Forge team uses Ansys Mechanical for its thermal analysis and ray tracing capabilities — another requirement that Bacon and his team had in order to advance structural, thermal, and optical performance.
“When we’re doing a thermal model it’s really important to be able to do ray-traced thermal modeling so we can see because we have deployable solar panels which shade part of the platform, so we need to be able to understand that and then overlay the thermal input from reentry,” says Bacon. “So being able to input lots of interfaces and handle our geometry — a very detailed model with quite thin elements in the solar arrays — and have a good meshing tool with Ansys Mechanical was very important as well.”
The team most recently used Mechanical to model stresses when developing a sea vehicle that serves as a water-based net. The team playfully refers to it as “the fielder” since its concept bears a similarity to the catcher position in the game of cricket.
Saltwater is damaging to the satellite but the fielder serves as a buffer, “catching” the vehicle as it lands at sea. The sea vehicle is lightweight and highly maneuverable but must be durable enough to withstand impact, even if the satellite lands at 20 miles per hour.
As Space Forge continues to grow their business, Bacon and his team expect to manufacture at scale in another five years. They also plan to keep Ansys’ simulation on board as an integral part of operations.
“A lot of advanced simulation software has been written by scientists and scientists are fantastic at many things, but user interface development is not usually one of them,” says Bacon. “Ansys is a great balance among performance, accuracy, capability, and usability, which you don’t get with a lot of packages — you usually get two out of the four.”
Bacon is looking forward to further exploration using Ansys’ software, including analyzing and simulating the crest points of waves created by “the fielder” during landing, the net itself in more detail, and the interiors of all the satellites in the ForgeStar’s fleet.
“You’re transitioning through a whole range of different speeds and altitudes and it’s really important that your vehicle is stable. We looked at which software could model anything from sea level up to hypersonic speeds and Ansys won that trade-off with its computational fluid dynamics (CFD) and Ansys Fluent in terms of what range it can simulate and what kind of geometry it can handle.”
— Andrew Bacon, Co-founder, Space Forge
“Ansys is a great balance among performance, accuracy, capability, and usability, which you don’t get with a lot of packages — you usually get two out of the four.”
— Andrew Bacon, co-founder, Space Forge
For more information about the Ansys Startup Program, review product details and program eligibility here.