Stability Under Pressure
Suction pile design is straightforward, but overdesign can be costly. Even small changes can generate significant savings.
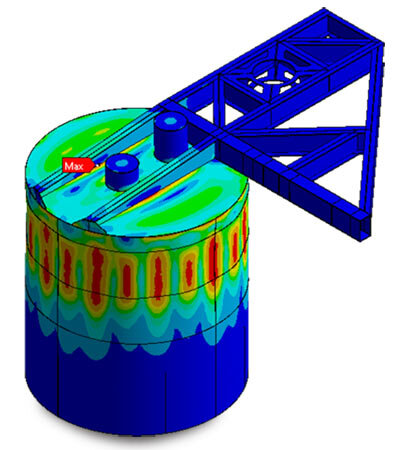
Suction piles provide a solid foundation for offshore energy structures, but overly conservative material specifications can increase project costs unnecessarily. Ansys elite channel partner EDRMedeso used structural simulation to help oil and gas companies better understand how the sea floor interacts with pile structures to save costs.
With winds, waves and ocean currents all capable of shifting offshore energy facilities off course, seabed anchoring is essential for safe, productive operations. Keeping large structures moored in place is no easy task, however. And that is especially true as the oil and gas industry explores water depths where conventional pile driving or gravity-based loading is not possible.
In those environments, suction piles are a proven alternative. They provide a reliable subsea anchor for production platforms, offshore drilling units, exploratory vessels, floating production and storage offloading (FPSO) units, and other facilities in water depths up to 3,000 m. They also secure fixed and floating wind turbine installations, even in shallower waters.
Described informally as resembling overturned buckets, suction piles are in fact large-diameter, hollow steel cylinders with a sealed top and an open bottom. Embedding them into the sea floor is a multistep process: First, crews allow the suction pile to drive itself into the soil using its own weight, then they pump water out of the suction port. This creates differential underpressure that pulls the pile to its set depth, leaving the top flush with the seabed and providing significant foundation capacity.
Because suction piles rely on the soil around them for their holding capacity, understanding how they interact with the surrounding sea ground is a key design consideration. For more than a decade, TechnipFMC has used Ansys structural simulation software to analyze suction pile/soil interaction. In this case, engineers used Ansys Mechanical on a North Sea project, performing a 3D stability analysis that included a more physically correct simulation on suction pile nonlinear interaction with the sea ground. By better predicting soil behavior during suction pile installation, Ansys Mechanical helped prove that thinner-walled suction piles could be deployed without buckling under pressure, enabling the development of more efficient, lighter and less costly technology.
Finite element mesh of a suction pile
“The oil and gas industry explores water depths where conventional pile driving or gravity-based loading is not possible.”
Soil is the stabilizing structure for suction piles, but offshore soil profiles, soil resistance and mechanical characteristics vary widely around the world and respond to loading conditions in unique ways. Depending on the seabed soil, it can take varying amounts of pressure to embed the suction pile, so it must be designed to withstand the pressure required to pull it down or it will collapse. In general, very stiff soil provides more support and reduces the likelihood of the suction pile buckling. On the other hand, very weak soil has a lower buckling threshold.
In the past, the interaction between the suction pile and the sea ground was often simulated by radial springs with nonlinear stiffness. However, this procedure can describe phenomena only in a simplified manner and results in very conservative — even uneconomic — design solutions incorporating thick-walled steel. Since the average suction pile is 10 to 12 m long and 6 to 7 m in diameter, and certain foundation bottom structures have as many as four suction anchors, the ability to reduce the thickness even a few centimeters can result in considerable material savings. In a North Sea project, using Ansys Mechanical simulation reduced TechnipFMC’s steel cost by NOK 2.5M ($281,504 USD).
To verify the three-dimensional behavior of the soil during soil–pile interaction, EDRMedeso engineers used the finite element analysis tools and geomechanics library in Ansys Mechanical, which analyzes rigid and flexible bodies within a single solver. Ansys Mechanical leveraged Dynardo’s multiPlas software, which is now included in the Ansys Mechanical geomechanics toolbox, to examine elastoplastic material behaviors.
By Frode Halvorsen, Head of Technology Innovation, EDRMedeso, 2020.
Buckling mode (top) and von Mises stresses (bottom) to determine the ultimate strength of a material and identify the point at which it will collapse.
Specifically, the simulation engineers:
Modeled a quarter-scale integrated template structure with soil surrounding and filling the interior of the suction pile
Generated a mesh of the entire assembly
Performed nonlinear buckling analysis and gradually increased suction pressure
To validate the suction pressure capacity, engineers increased soil spring stiffness according to DNV GL specifications. The suction capacity obtained with various soil spring stiffnesses verified higher buckling resistance at increased working loads, providing confidence in the simulation and in the efficacy of thinner-walled suction piles.
Suction piles offer considerable advantages compared to other deep foundation technology. They are easier, less expensive and less time-consuming to install and require minimal seabed preparation. Suction piles are also environmentally sound — installation is so quiet it does not disturb marine life. Removing them after decommissioning is simple and leaves no metal behind.
Suction pile design is straightforward, but overdesign can be costly. Even small changes can generate significant savings. By showing a higher model-predicted failure load than previous calculations allowed, EDRMedeso and Ansys Mechanical helped TechnipFMC eliminate conservatism in material selection while enabling significantly increased working loads and improved design and installation economics.
“Ansys Mechanical has enabled TechnipFMC to optimize suction pile design toward a more realistic solution,” said Nuno Vaz, who works in Lead Structural Design Engineering, EMS Analysis Well Control at TechnipFMC. “Combined with the current Dynardo soil material model, it has given us more confidence about suction pressure limitation during installation.”