Time-to-market is crucial for crane manufacturer HMF Group
HMF Group is an international company that develops, manufactures and markets high quality truck-mounted cranes.
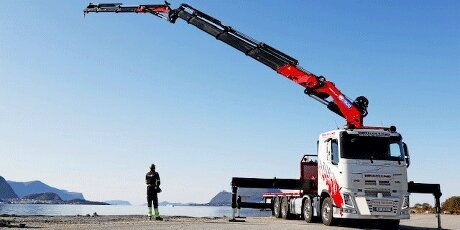
Cranes from HMF Group are composed of complex geometries that interact with advanced hydraulic systems as well as software systems which means that the product development cycle of a new crane is somewhere between 2-3 years. Consequently, the development department at HMF Group – which consist of about 40 professionals – are always searching for new tools that can potentially shorten the development phase. If HMF Group can get new crane models through the development and testing phases faster, both earnings and competitiveness will be improved.
At HMF Group, the development department have used simulation tools for many years and run FEM simulations continuously to verify their designs. In their never-ending search for improvements, HMF Group decided to invest in ANSYS Mechanical. Here, HMF Group worked closely with EDRMedeso and their consulting and training services.
“ANSYS is a very comprehensive and complete simulation program, and one of the main advantages is speed. Our simulations and analyzes are simply faster when using ANSYS. If we can reduce the development time by just 3-7 percent – and those are the preliminary indications – it is worth the entire investment,” says Torben Wittendorff Andersen, Head of Projects at HMF Group. He explains that ANSYS is structured differently with several options for different design scenarios, and this gives the users clear answers much faster.
“Our simulations and analyzes are simply faster when using ANSYS.”
— Torben Wittendorff Andersen, Head of Projects at HMF Group
When it came to the implementation of this advanced simulation tool, HMF Group turned to EDRMedeso. Thus, eight designers from HMF Group completed EDRMedeso’s ANSYS training. With the training and implementation complete, many simulation tasks have already been transferred to ANSYS. This leads Torben Wittendorff Andersen to conclude that ANSYS will most likely be the preferred tool for simulation moving forward.
“The comprehensive ANSYS training from EDRMedeso gave all of us a thorough introduction to and understanding of the possibilities and functionality in this advanced tool – and we appreciate the direct line to EDRMedeso and their skilled experts in case of support needs,” says Torben Wittendorff Andersen.
HMF Group is using simulation to locate the stress peaks and hotspots that may need to be addressed. A hotspot is an area where high tension is concentrated around a smaller area and therefore potentially a weak point.
“Our products are dimensioned in relation to fatigue, so it is very important to keep track of all hotspots. Perhaps a crane can lift a given weight effortlessly the first 1,000 times, but it should be able to withstand up to +150,000 lifts depending on the type of product application, and here the simulation tool will help us tremendously with these predictions, because we can quickly identify the problematic areas where we must go deeper.”
At the very end of the development cycle, HMF Group perform a physical fatigue test on an entire crane to ensure it has the required strength. First, there is a dynamic test procedure with several thousand lifts with a lifting moment of at least 125 percent. This is followed by a 3-6-month testing period in the field, where the crane is exposed to many demanding tasks.
According to Torben Wittendorff Andersen, this is where HMF Group can save both time and money, because if there is a breakdown or any indications of a problem in the physical test, it will prolong the development cycle and thus time-to-market.
“We are occasionally experiencing problems during the physical tests, although it is less frequent. However, when it does happen, we can easily lose a month or more because a component needs to be re-engineered which is very costly. So, if we can simulate quickly and accurately how a new crane is loaded with strength, this will increase the likelihood that the crane will pass the final fatigue test. The projects we have run so far using ANSYS have been implemented faster and without design relapse. I therefore strongly believe that ANSYS will reduce the risk of design errors and thus contribute to increased profitability for HMF Group,” Torben Wittendorff Andersen concludes.