Top 5 Features in Ansys Mechanical 2023 R1
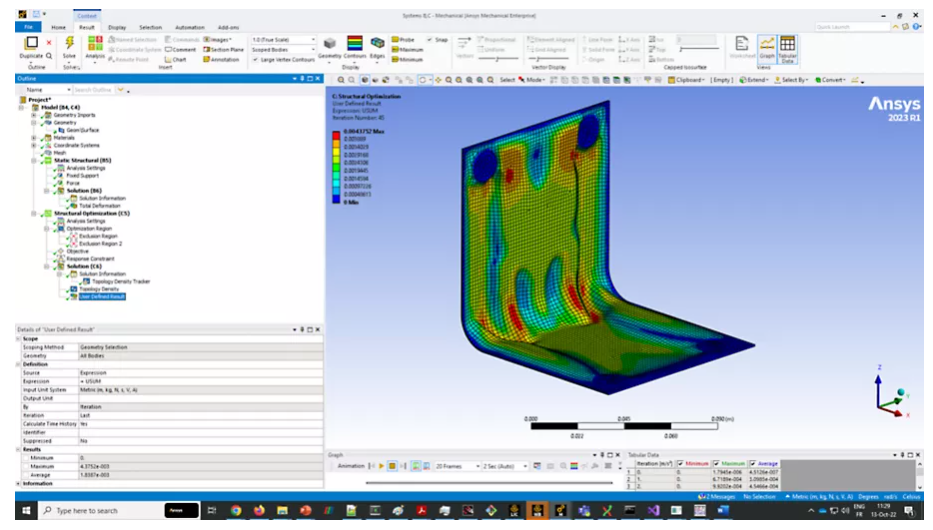
Ansys 2023 R1 focuses on enhancements that enables you to achieve more efficient and accurate finite element analysis (FEA) simulations using Mechanical, including:
Geometry based reassociativity (GBA)
Resource prediction
Geometry preserving mesh adaptivity (GPAD)
Topography optimization
Contact setup
Mechanical is known in the industry for its ability to work with the underlying geometry through meshing, setup, and solving. Longtime users may know when making edits to geometry that associativity in Mechanical can potentially be lost, and previously defined settings in Mechanical can become underdefined. Ansys Workbench has had capabilities to reassociate model settings after geometry changes, but the process was not always foolproof.
No longer are the days of making a change and seeing a tree full of question marks because of lost associativity. In 2023 R1, you can efficiently make edits to a model and use the new Scoping Wizard tool to automatically detect and reestablish scoping.
Now, when importing an updated model back into Mechanical, different parts of the geometry will be colored depending on the associativity. You can then work your way through the list to visualize what has been reassociated and what hasn’t. Items that are found and can be reassociated are colored green, items with multiple matches are colored yellow, and items that are unable to be reassociated automatically are colored red.
Figure 1. Efficiently reestablish associativity after editing a CAD model using the new Scoping Wizard.
Have you ever had to solve a complex model in Mechanical that you either weren’t familiar with or didn’t have prior knowledge of the critical stress and strain areas? In the past, there were two methods to approach this:
Generate a coarser mesh, solve the model, and add refinement to areas of importance.
Generate an overrefined mesh from the start to accurately capture the areas of importance.
We understand these methods can become time consuming, so we’ve introduced a new feature to improve efficiency for durability studies. This new feature, geometry-preserving mesh adaptivity (GPAD), eliminates the need for an overrefined initial mesh and takes out the guesswork on mesh sizing.
GPAD enables you to start a simulation with a coarser mesh, and, as the model is solved, the solver monitors quantities like variation of stress in regions and automatically refines the mesh. The refinement of the mesh occurs by matching itself with the underlying computer-aided design (CAD), working closer to the true shape of the model rather than basing it off the previously solved coarse mesh. Because the remeshing occurs during the solution phase, it improves accuracy without incurring a great deal of computational penalties.
Geometry-preserving mesh adaptivity (GPAD) automatically refines a mesh based on the initial CAD geometry.
FEA simulations are becoming larger and more complex due to different types of elements, materials, contacts, joints, boundary and loading conditions, and more. At the same time, use of high-performance computing resources is growing exponentially, both on-premises and in the cloud. At this stage, it is extremely important to know hardware requirements such as memory and the number of central processing units (CPUs).
In this cost and time-sensitive world of simulation, it is important to understand the optimal number of CPUs that will provide maximum scaling to drive efficiency of time and cost. Enhancements to resource prediction now enable you to solve this problem by predicting the required memory, solve time, and solver scaling performance before solving the problem.
Resource prediction uses ML-based algorithms to predict memory and solve time for complex simulation models. This algorithm analyzes millions of anonymous data points from previously solved simulations and compares that data to the model the user solving to come up with the desired prediction. This feature works with linear static and modal analysis with both iterative and direct solvers and provides scale-up performance of up to 32 cores, as of Ansys 2023 R1.
Figure 2. Leverage artificial intelligence/machine learning (AI/ML) to gain insight into the computational resources required to solve an Ansys Mechanical simulation.
Over time, different optimization techniques have been incorporated into Mechanical, such as parametric study, topology optimization, lattice optimization, and shape optimization. In 2023 R1, we are coming up with a new capability called topography optimization.
Fabricated structure design performance heavily depends on mass, especially when the structure is undergoing dynamic loading; therefore, weight reduction is crucial. With thin structures, we cannot apply topology optimization, and other methods are less efficient in finding a solution — especially when we have assembly and design constraints.
Topography optimization works best in this type of scenario, in which we are not changing the thickness or shape of the design, but are using free morphing techniques to identify optimal locations of mesh nodes. Different controls can be used to make sure that the design is manufacturable. This approach helps improve noise, vibration, and harshness (NVH); fatigue; crash performance; and/or can reduce the weight of the structure.
Figure 3. Optimization of frame and shell structures can now be performed using topography optimization.
For automotive users, contact setup for body in white (BIW) simulations can become a very cumbersome process. This is mainly because these BIW simulations involve a variety of intricate features and a variety of different contact types, including adhesives, welding, riveting, and more. In the past, a lot of manual bookkeeping was required to create multiple contacts so users could set up contacts on the correct sides of their shells.
Enhancements in this release now simplify setup by specifying that the target surface is, in fact, double-sided. It accounts for both the positive and negative normal target surfaces and removes the need to create multiple contact definitions.
Figure 4. Contact enhancements now simplify the setup for complex models, like contact between adhesives and metal sheet components.
Check out our What’s New in Ansys Mechanical 2023 R1 video.
For an in-depth update on the five features discussed in this blog, as well as all the other new features in Mechanical, register for the on-demand webinar Ansys 2023 R1: Ansys Mechanical What’s New.