UK schoolboy designs and 3D prints one of a kind ‘unmanufacturable’ Aerospike rocket
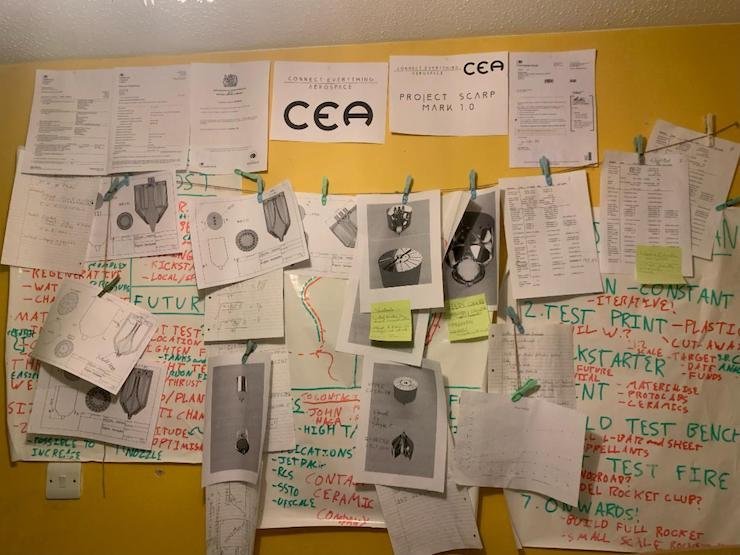
During the UK lockdowns, high-school student Ewan Craig turned to learning about rockets after he finished his required studies and dove into the mysteries of propulsion and all things aerospace.
Ewan, then 16, signed up to a Massive Open Online Course (MOOC) offered by MIT, a free graduate-level introductory program on aerospace. The textbooks on offer through the course were supposed to be for older and more formally educated students than Ewan.
What drew him in was research from the 1950s-60s on a rocket system called the aerospike, first undertaken by Rocketdyne Propulsion and Power (now Aerojet Rocketdyne), a unit of the Boeing Company of California.
The engine had never been commercially developed, and Ewan wanted to understand why. The aerospike was conceived as a one-stage engine that could maintain aerodynamic efficiency throughout its flight by adapting to the changing altitudes of the craft it thrust into space.
A vehicle with an aerospike engine uses 25–30% less fuel at low altitudes, where most missions have the greatest need for thrust; as a result, it can launch without boosters, a key time and cost-saver.
Technical challenges persist in creating an economical and manufacturable aerospike that can overcome the cooling issues inherent in its high-performance design.
Picture: Ewan Craig
“You have to model it computationally using CFD (Computational Fluid Dynamics) software. But the issue for me was that all the free, open-source software is for handling simple components and behaviours. By this point, my model had already reached six or seven million DOF (Degrees of Freedom),” said Ewan.
Ewan then formed his own company, CEA Space (Connect Everything Aerospace), and kept going. He reached out to Ansys, the software provider, through its contact page, hoping to unlock a few extra features or get a free-trial tool to meet his needs.
Ansys responded directly via partner EDRMedeso in the Advanced Manufacturing Park Technology Centre in South Yorkshire. EDRMedeso began a helping hand relationship that introduced Ewan to high-end modelling and simulation.
“I reached out to several 3D metal print manufacturers in order to understand what was possible,” Ewan said. “There was not much assistance of any type. People quoted me 30, 40 thousand pounds sterling for a single print. The other issue was their saying that they couldn’t do the aerospike print at all. That was a nightmare.”
Ansys suggested that Ewan consider the company Velo3D, a company that has previously provided 3D printers for companies such as Primus Aerospace. Velo3D engineers helped Ewan with design suggestions and offered a free test print.
Ben Wilson, Applications Development Engineer for Velo3D said:
“With the capabilities of our AM system, we didn’t need to make overly invasive modifications to the original part in order to make it printable. After a few iterations, we had a rocket that could be printed successfully without any manual support removal needed.”
Picture: Aerospike design
The manifold ring, where all of the passages converge, is a mid-sized circular passage that is routed in a complete circle around the part,” said Wilson.
“The closures at the tops of passages would likely be very rough on other systems and may have some partially melted particles that are prone to falling off as FOD (Foreign Object Debris) in operation.”
Ewan avoided Design for Additive Manufacturing (DfAM) rules that compromise many advanced designs. Ewan’s design required a cooling system for the combustion chamber and central aerospike, which meant a channel within a channel, effectively an unsupported wall within an unsupported wall, which is what a lot of manufacturers had told him was impossible.
The design has been optimised and printed, and will soon be test fired at an American university that contributes to progress in science and aerospace.
Ewan said: “If you can provide an affordable solution to propulsion for launch vehicles, which I believe AM can, then there is a greater opportunity for smaller businesses to make breakthroughs in space travel and commercial aerospace. I’m very hopeful about the changes ahead—and for engineers like myself to be invited to make a potential impact.”