In the field of medical device manufacturing, precision in optical design is not just a benefit—it’s a necessity. As this industry increasingly relies on advanced optical systems for diagnostics and treatment, precise tolerancing becomes essential. This practice, which establishes acceptable limits for deviations in design parameters, ensures that optical products meet strict performance specifications and remain practical to produce. This article explores the pivotal role of tolerancing in optics, particularly within the medical devices sector, and highlights how Zemax OpticStudio, a premier Ansys software, empowers engineers to navigate its complexities and effectively bridge the gap between theoretical designs and real-world applications.
Tolerancing in Optics and Photonics Design
What Is Tolerancing in Optical Design?
In the precision-driven field of Optics, maintaining ideal design specifications is crucial for optimal performance. Yet, manufacturing and assembly processes introduce deviations or ‘errors’ from these ideal specifications, which will degrade the performance of the optical system, significantly if the design is sensitive. Examples of these errors include variation of lens thickness (fabrication errors) or misalignment with the mechanical axis (assembly errors).
Tolerancing, therefore, is a systematic approach to analyze the system sensitivity to these deviations and determine the maximum allowable error that can be introduced into the design whilst meeting the performance specifications.
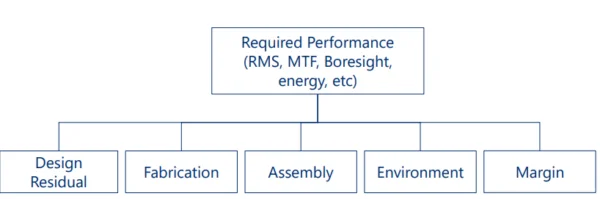
Sources of error (error budget) on the optical performance
Why Is Tolerancing Crucial in Optics?
Tolerancing allows optical engineers to quantify the effects of errors, enabling them to predict performance variability across production batches i.e. the yield. This ensures that a significant proportion of manufactured devices meet the necessary design criteria. This critical analysis is not solely about leveraging optical engineering knowledge; it also necessitates collaboration with mechanical and optical test engineers to tackle the complex challenges of manufacturing and assembly. Examples include precision in high-performance cameras or the high-precision required in laser systems used in medical procedures, where small errors can lead to significant functional issues.
By serving as a bridge between theoretical designs and their practical applications, tolerancing is pivotal in ensuring the reliability and efficiency of optical system production. As technology advances, the role of digital tools and computational modeling in enhancing tolerancing techniques continues to grow, shaping the future of optical design.
The Crucial Role of Tolerancing in the Medical Devices Industry
Why Is Tolerancing Needed in the Medical Devices Industry?
In the medical devices industry, tolerancing is crucial for ensuring the safety and efficacy of diagnostic and surgical instruments. Here are reasons why:
- Precision and Predictability: Tolerancing guarantees that optical components – such as lenses, mirrors, and sensors – are manufactured and aligned within specified limits. This precision ensures that medical systems perform as expected, delivering predictable results critical in healthcare settings.
- Optimal Performance: Medical devices consist of various interacting components. Proper tolerancing ensures these parts are precisely positioned and aligned, optimizing the device’s overall performance. This is especially vital in instruments where even minor deviations can lead to significant consequences.
- Reliability and Safety: The specifications for medical applications are strict. Tolerancing minimizes variability in component quality and alignment, reducing the risk of malfunctions or inaccuracies. This not only enhances the reliability of medical instruments but also safeguards patient safety, a paramount concern in medical procedures.
- Cost-Effectiveness: While tighter tolerances typically necessitate more precise manufacturing processes and higher-quality materials – thus increasing production costs – effective tolerancing can also include the use of compensators. These allow for relaxations in tolerances without compromising performance, providing a cost-effective solution that balances quality with production expenses.
Therefore, tolerancing in the medical industry is essential for maintaining high standards of device performance and patient safety, while also considering production costs.
What Are the Major Pain Points of Tolerancing within The Industry?
For tolerancing, we need to calculate the error budget which defines the maximum error that can be introduced during each step of the design, manufacture, assembly and operation. Managing this for multi-component systems and ensuring high yield for mass production, while mitigating the costs associated with high-precision manufacturing is a massive challenge for optical and mechanical engineers.
In the tolerancing process itself, we need to find out what can go wrong for the design to deviate from the ideal and how to account, and if possible, to correct for these in the simulation. Therefore, for large and complicated optical systems one can imagine that not only is there a potentially huge number of tolerances to keep track of, but also to ensure they are implemented correctly in the simulation. This can be an extremely manual and time-consuming task with the potential for error and long simulation run times during tolerance analysis, sometimes taking longer than all of the other design stages combined!
Examples of systems where tolerancing can be especially painful are:
- Large systems with multiple components and lens elements: in these systems there will be multiple sources of error and may be more sensitive to errors due to a balancing of aberrations.
- Systems with off-axis components: knowing where to apply the misalignments and perturbations requires information on how the components are mounted and information from the manufacturer. These systems may also be more sensitive to tolerances.
- Double Pass Systems: Great care needs to be taken to ensure these systems are set up correctly in simulation for tolerancing.
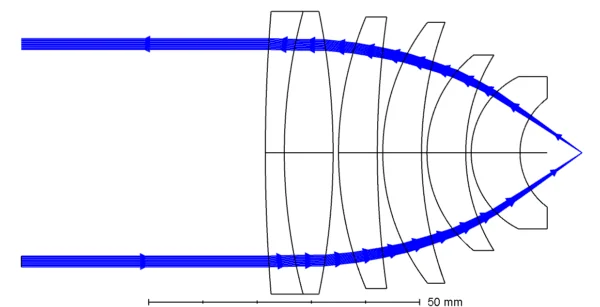
Example of double pass system: aplanatic laser beam delivery system
- Aspheres and Freeform components: Custom lens surfaces are increasing in popularity and they have many key differences with standard lenses. Their unique design challenges mean these components require more specialized and tailored tolerancing procedures.
How Zemax Solves Tolerancing Issues in Medical Devices
How Does Zemax Address Common Tolerancing Challenges?
Zemax OpticStudio provides flexible tolerance development and analysis capabilities to easily incorporate the effects of fabrication, assembly and environment into an optical design. Here’s how Zemax effectively tackles the challenges:
- Fast initial set up of tolerances: OpticStudio has a Tolerance Wizard interface for users to quickly generate initial tolerances. The user can also use Tolerance Presets to instantly set up tolerances with realistic values from lens vendors including Optimax, EdmundOptics and Asphericon for varying grades of precision. Furthermore, the user can select the tolerance criterion from a large number of presets including spot size, MTF, boresight error and many more.
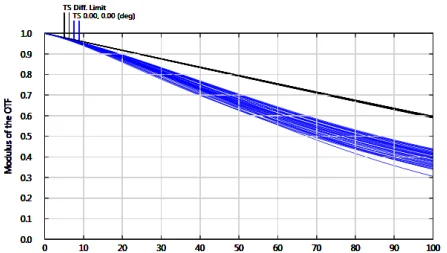
Impact of tightening tolerances with ‘Precision’ Grade on MTF performance of imaging system
- Smart Tools to Speed Up Tolerancing: Zemax includes tools like Paraxial Focus Compensation, Quick Sensitivity, Quick Yield, Tolerance Cache, and Polynomial Sensitivity to improve speed and reduce computational effort.
- Operands and Features Aimed at Simplifying Tolerancing: There is a large library of existing tolerance functions or ‘operands’ to automatically implement tolerances of different parts of the optical system. These include operands that incorporate tolerances on lens and mirror surfaces, material, roll, decenters and tilts and many others. Furthermore, Zemax Optic Studio continuously updates its software with new features and operands to simplify the tolerancing process for increasingly complicated designs. For example, the Composite Surface’ feature is very powerful for the user to easily tolerance irregularities of freeform surfaces.
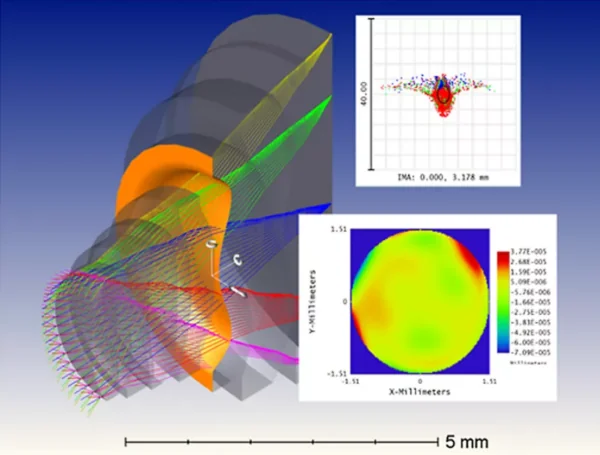
Ansys Zemax OpticStudio includes enhanced composite surface capabilities
- User-Defined Tolerance Operands: In addition, Zemax Optic Studio has user-defined operands to specify custom tolerances. This is particularly useful in complex systems, such as double pass systems and those with off-axis components to account for all of the real degrees of freedom in manufacture and assembly.
- Increased Flexibility with Tolerance Scripts: Users can write custom scripts to define the tolerance procedure which can simulate a multi-step process during assembly and with each step adding or removing different compensators and using different (user-defined) tolerance criterion which can be monitored and reported.
- Flexible Set-Up of Compensators: Zemax uses its in-built optimizers to ensure that the compensators compensate for the limiting tolerance and users can define any parameter to be a compensator.
- Yield Optimization: In Zemax Optic Studio, there is a powerful feature called “Improve Manufacturing Yield” Optimization Goal which targets less sensitive systems during optimization. The user can also call the tolerancing process during optimization to design for best estimated performance.
How Does Zemax Differ from Other Optics Solutions?
Zemax Optic Studio stands out among optics solutions due to several features and advantages:
- User-friendly interface: Zemax has a more intuitive GUI for imaging system design, making it easier for users to familiarise with the software
- Extensive online resources and training: There are lots of online resources, technical support, existing examples and forums to help users quickly find solutions. In-depth training on Zemax OpticStudio is also available in the Ansys Learning Hub where there is unlimited access to classroom, virtual and self-paced learning courses.
- Design template library: Zemax offers solutions for users to avoid reinventing the wheel with almost 650 existing design templates to get started with their designs right away.
- Programming Interface: In addition to the Zemax Programming Language (ZPL) interface, full flexibility of OpticStudio is available by utilizing ZOS-API scripting with Python, C++, Matlab and others. Here users can create custom functions and extend the capabilities of the software to meet their specific needs.

Programming features available
- CAD Integration: In Zemax, the user can import and export CAD files which are obtained via collaboration with mechanical engineers, ensuring that optical designs can be integrated smoothly into larger mechanical systems.
- Automatically Generate ISO10110 and Mechanical Drawings: The user can quickly generate ISO10110 compliant drawings with tolerance information and other mechanical drawings necessary for optical shop fabrication, ensuring that designs meet industry standards.
- STAR Module: This award-winning module (OpticStudio STAR Module from Zemax, an Ansys Company, Wins Coveted SPIE Prism Award in Software) is an integrated workflow that streamlines the data import of FEA data into OpticStudio to perform structural, thermal and optical performance (STOP) analysis due to structure and thermal deformation in optical system to visualize the environmental impacts and reduce the risk of errors associated with real life conditions.
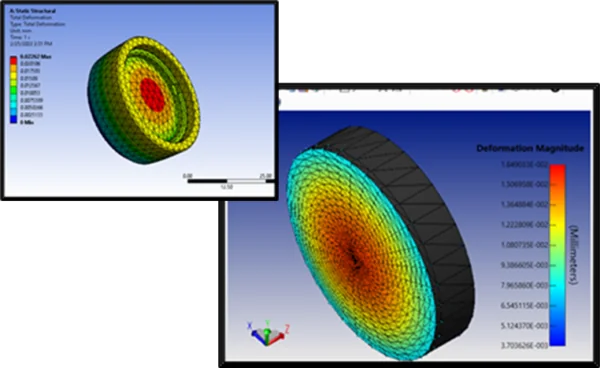
STOP analysis of cemented optics for high-end imaging system
- Interoperability: OpticStudio supports interoperability with other engineering tools such as Ansys Lumerical, allowing seamless integration into the overall product design and development process.
Zemax OpticStudio distinguishes itself as a leading optics solution that offers a comprehensive suite of features designed to streamline the optical design and tolerancing process. These features provide unparalleled support for engineers aiming to push the boundaries of what’s possible in optical design.
Conclusion
The precision and reliability of optical systems are foundational to their success across various industries, especially in fields requiring the highest standards of performance and safety, such as in medical engineering. Tolerancing, facilitated by advanced tools like Zemax OpticStudio, plays a crucial role in bridging the gap between theory and the real world encountered by mechanical and optical test engineers to optimize for the best manufacturable design. Looking forward, with advancements for example in freeform optics and the increasing use of metalenses and photonics, there will be an increasing need for automation, increased efficiency and enhanced predictive capabilities of the tolerancing process.
Found this article interesting? Join our next Ansys Zemax webinar on September 10 on the topic “Designing Endoscopes Using Ansys Zemax OpticStudio”
Learn more and sign up for the webinar