AFRY is pioneering safety in hydrogen energy systems using Ansys Fluent
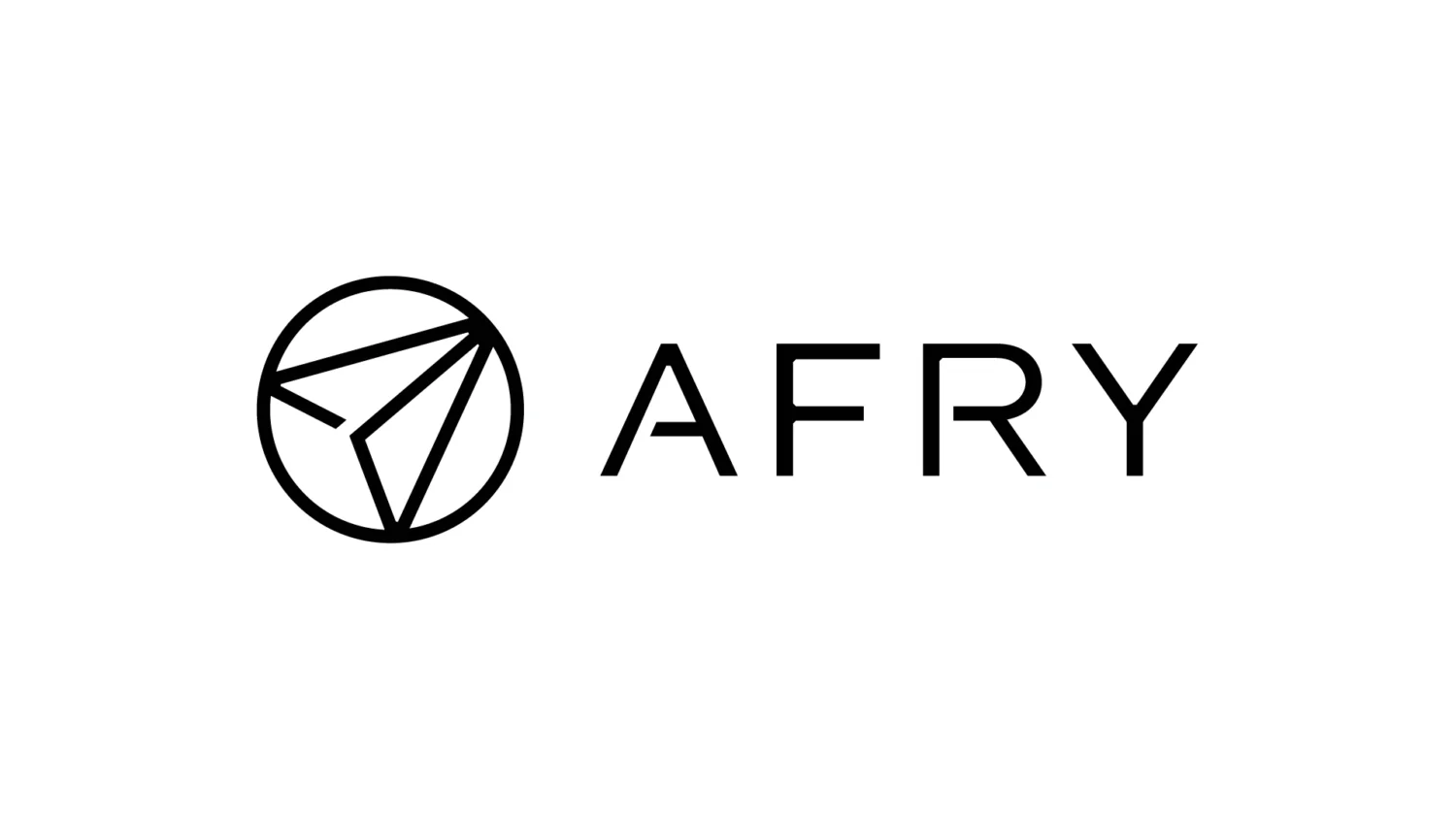
Hydrogen, a promising alternative to fossil fuels, poses significant risks due to its unique properties. Stored at pressures of up to 700 bar, its low volumetric energy density (see Figure 1) and high diffusivity make it prone to leaks and catastrophic failures. If a hydrogen fuel system ruptures, the consequences are severe:
AFRY sought to understand these risks in confined spaces, such as bus depots, where multiple high-pressure hydrogen cylinders are stored. The goal was to assess these dangers, design mitigation measures, and protect lives and infrastructure. Ensuring the safety of hydrogen systems is critical also for public acceptance and the sustainable rollout of hydrogen-based infrastructure.
Figure 1, volumetric energy density of different fuels.
Figure 2, simulated model.
To address these critical safety challenges, AFRY utilize Ansys Fluent to analyze the propagation of shock waves and the dispersal of hydrogen-air mixtures in the event of a rupture. The analysis modeled the rupture of a high-pressure hydrogen supply, see Figure 2 line and the resulting shockwave propagation, gas dispersion, and explosion risks. Key features of the simulation included:
Using a coupled solver for compressible flow and advanced combustion modeling (e.g., hybrid eddy dissipation and finite-rate chemistry), the simulation modeled transient, reactive multi-component gas behavior. A detailed mesh of 18.7 million polyhedral cells, see Figure 3 captured complex dynamics, such as maximum peak pressures and hydrogen jet flow velocities. This simulation helped visualize risk zones, evaluate safety thresholds, and test scenarios for secondary protective measures like pressure relief valves (PRVs), see Figure 4. AFRY use Ansys Fluent for its precision in compressible reactive flows and its robust computational performance, ensuring actionable insights for hydrogen system safety.
Figure 3, mesh used for the analysis.
Figure 4, example of PRV protective casing.
Figure 5, pressure profile of a shock wave.
Figure 6, maximum simulated peak pressure.
The simulations yielded critical safety insights, including:
Rupture of fuel lines will have devastating consequences.
Person standing in the garage will be killed by the initial shock wave from the gas cylinders. Even without ignition of the hydrogen/air mixture.
Secondary PRVs and protection around fuel lines are necessary for safe operation of hydrogen powered vehicles.
Red area at 43 ms after fuel line rupture.
Above 300 mBar (30 kPa), 100% death indoors, severe damage on structures, red area.
By leveraging Ansys Fluent, AFRY enhanced its capacity to address hydrogen’s inherent challenges, safeguarding the future of this clean energy source. Without rigorous safety measures, hydrogen explosions can cause fatalities, massive structural damage, and widespread destruction. With Ansys Fluent, AFRY showcase the power of engineering simulation in safeguarding lives and enabling the safe adoption of hydrogen as a clean energy source.
This presentation was delivered by Christoffer Källerman at the EDRMedeso Meet the Experts Simulation Seminar in Gothenburg on November 12, 2024. With over 17 years of experience, Christoffer specializes in Fluid Mechanics and Business Development at AFRY, where he supports companies in driving product innovation and development. Leveraging Ansys, AFRY continues to advance the capabilities of simulation, delivering safer and more sustainable solutions.