Digital Twin Helps Skagerak Kraft optimize production and maintenance of hydropower plant
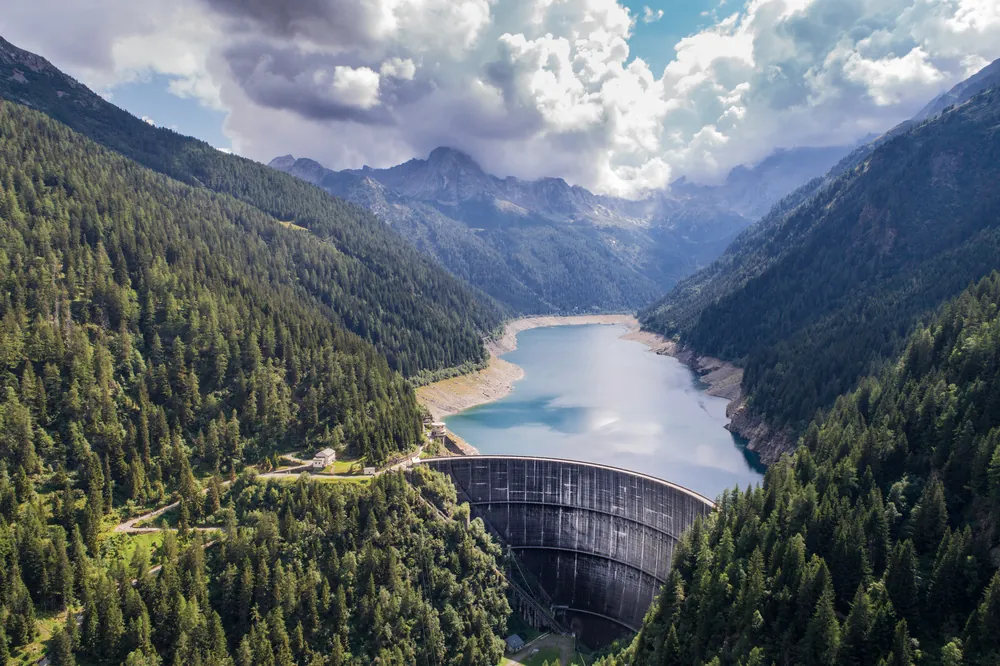
One of the biggest constraints of hydropower is aging production equipment. The aging hydropower park necessitates increasing maintenance needs, and the hydropower industry requires digitalization, standardization, and automation. The traditional approach with a “scheduled maintenance” methodology will be neither sufficiently cost efficient nor sustainable. This has sparked significant interest within the industry to develop new and digital solutions for condition monitoring, predictive maintenance, and operational optimization in hydropower plants.
In response to the issues faced, a collaborative research project between Norwegian energy company Skagerak Kraft and other players in the hydropower industry was initiated in 2021. The purpose? To explore the possibilities of increasing electricity production in existing hydropower plants through the use of smart digital technology. The project, named SmartKraft, is partly financed by Enova.
Skagerak Kraft approached EDRMedeso to provide a smart technical solution to tackle the issues. At EDRMedeso, we recognized the challenges and saw the potential in our Digital Twin solution to address the project and industry goals.
One common application for a Digital Twin is within the field of Predictive Maintenance, where sensor or control system data is fed from the physical asset to the Digital Twin – in real time. The Digital Twin has physics models, engineering know-how and data analytics embedded into the solution. This enables you to predict future performance, behavior, and maintenance needs, providing an invaluable resource for decision-making.
EDRMedeso identified the opportunity for using a Digital Twin as a copy of the actual hydropower equipment in the Cloud. Using this approach, Skagerak Kraft would be able to optimize their energy production by understanding exactly what’s happening with the equipment in operation, prevent damage, and better predict when maintenance is needed.
Skagerak made the decision to implement the Digital Twin for the Grunnåi power plant’s latest generator. This became the starting point of EDRMedeso’s work, creating a virtual model from data of the physical power plant.
The initial test models predicted various lifetime indicators in the runner, generator, bearings, spiral casing and shaft. In the ramp-up period, the team focused on the generator model, using a thermal model to estimate lifetime.
Now as Skagerak has access to the Digital Twin, their generator expert can ascertain the damage rate/accumulated damage of their different generators.
The success of the implementation of the Digital Twin in Gunnåi has the potential to evolve the hydropower industry. Implementation of Digital Twins for more components in the future, would see a move toward predictive maintenance as a normality, rather than an exception.
By using EDRMedeso’s Digital Twin technology, Skagerak Kraft is changing the game in hydropower. As Digital Twins become crucial tools for predicting maintenance needs, the whole industry is on the brink of unprecedented evolution. The success at Gunnåi isn’t just about reducing downtime and breakdowns; it’s a glimpse into a future where green energy is increasingly reliable. The path to predictive maintenance, guided by the capabilities of Digital Twins, promises a sustainable and efficient future for hydropower.