Durham Engineering: delivering insight for cost-effective vessel and pipeline design and development
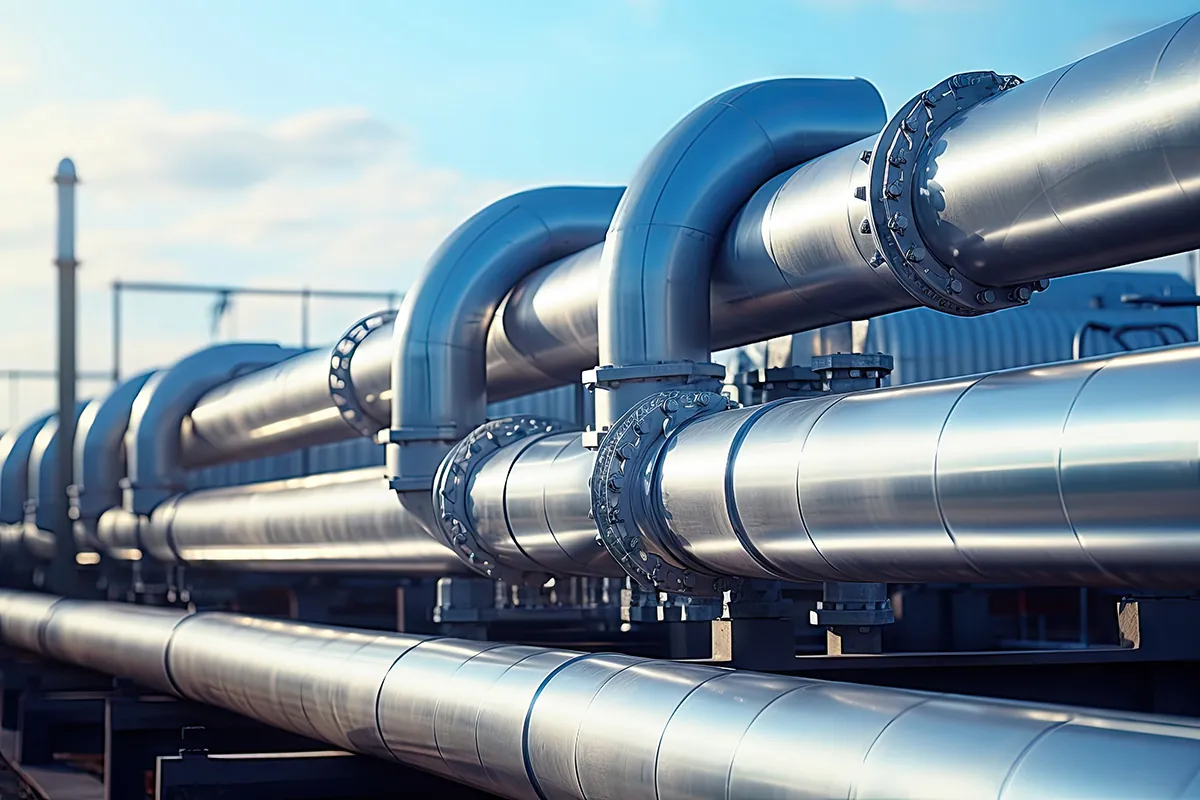
Durham Engineering’s customers often face challenges related to technical capability and the practical application of engineering knowledge. Many clients may have innovative ideas or specific process requirements but lack the expertise and resources to turn these concepts into reality. Additionally, many of these companies need to make modifications to ageing equipment where there is often a lack of technical data available and where the key objectives are cost-effectiveness and minimizing operational downtime.
These challenges highlight the need for tailored engineering solutions and support in realizing clients’ requirements, in a highly regulated environment. A recent project has involved a polyurethane and vehicle additive manufacturer who was looking to update safety systems on several ageing vessels. Although fitted with pressure relief devices, these did not meet the legislative requirements for flame engulfment and subsequent catastrophic explosion risks. In order to meet these requirements, bespoke safety nozzles were needed, the installation of which meant draining the tanks of all flammable toxic, noxious substances and fluids. Due to equipment age, degradation and potential human health and safety risks, the only option for assessment was to employ structural simulation, using finite element analysis tool, Ansys Mechanical.
Dating back to the 1960’s, technical data for the tanks was near non-existent and although regular maintenance had succeeded in keeping the vessels functional, these necessary modifications would require additional engineering analysis. The first challenge was that being so old, there were no benchmark calculations or code-recognized geometries that were applicable to the tanks. Therefore the tanks would need to be subjected a ’first principle’ analysis approach to form the basis of their appraisal. Each calculation would be highly conservative, idealised, and consequently not reflect reality. In this particular case, the expected solution was to drain the tanks, remove any traces of noxious materials and gases prior to any maintenance taking place as the projected size of the new nozzle meant any installation required a cut in the tank to fit new nozzles to suit the relief valves. Not only would this be a costly exercise due to equipment downtime, but it would be fraught with danger as engineers needed to enter the tank.
By using Ansys Mechanical, not only was the objective met but the simulation identified that the modification didn’t need to be as extensive as first thought. Using the predictive analysis of simulation, consultants at Durham Engineering were able to determine the maximum internal and external pressure limits of the vessel and a more appropriate-sized relief valve was selected, meaning existing openings could be used, thereby reducing the time the tanks were out of commission, but also negating the need for drainage and any higher risk human intervention.
The benefits of using simulation in this scenario are numerous. Durham Engineering successfully deployed a solution to their customer that delivered significant insight that helped:
Minimize cost and supply issues of downtime
Speedy payback – simulation costs were offset within a short period of time
Provide insight that would otherwise be unknown and cannot be achieved by traditional, first principle methods
Gain regulatory approvals
Highlight alternative solutions without physical prototypes or costly over-engineering
Provide safe assessment alternatives to inhospitable and hazardous environments
Illustrate engineering solutions to non-experts
Simulation and analysis of vessels and tanks helps the engineering and design process in a variety of ways, including validating engineering models, visualizing how objects deform under pressure and load, and aiding in client communication. Modelling allows for a comprehensive understanding of equipment performance, and helps clients visualize the behavior of the designed systems. Additionally, simulation can indirectly save money by streamlining processes and potentially reducing the time required for complex engineering tasks, ultimately contributing to cost-effectiveness.
Simulation also aids in meeting financial and legal obligations by providing evidence of diligence in employing technically competent engineers, as well as demonstrating compliance with design codes and safety requirements.
This example showcases the technical and financial impact that Mechanical Engineering can have on aging plant and equipment. However, when the required engineering pushes the boundaries of existing design codes and traditional analysis, it is invaluable software such as Ansys Mechanical that allows Engineers to confidently assess existing equipment and to overcome technical challenges.
– Andrew Lawson CEng IMechE Meng / Managing Director / Durham Engineering