STILFOLD: Redefining Metal Fabrication – The Sustainable Edge of Simulation Powered Design
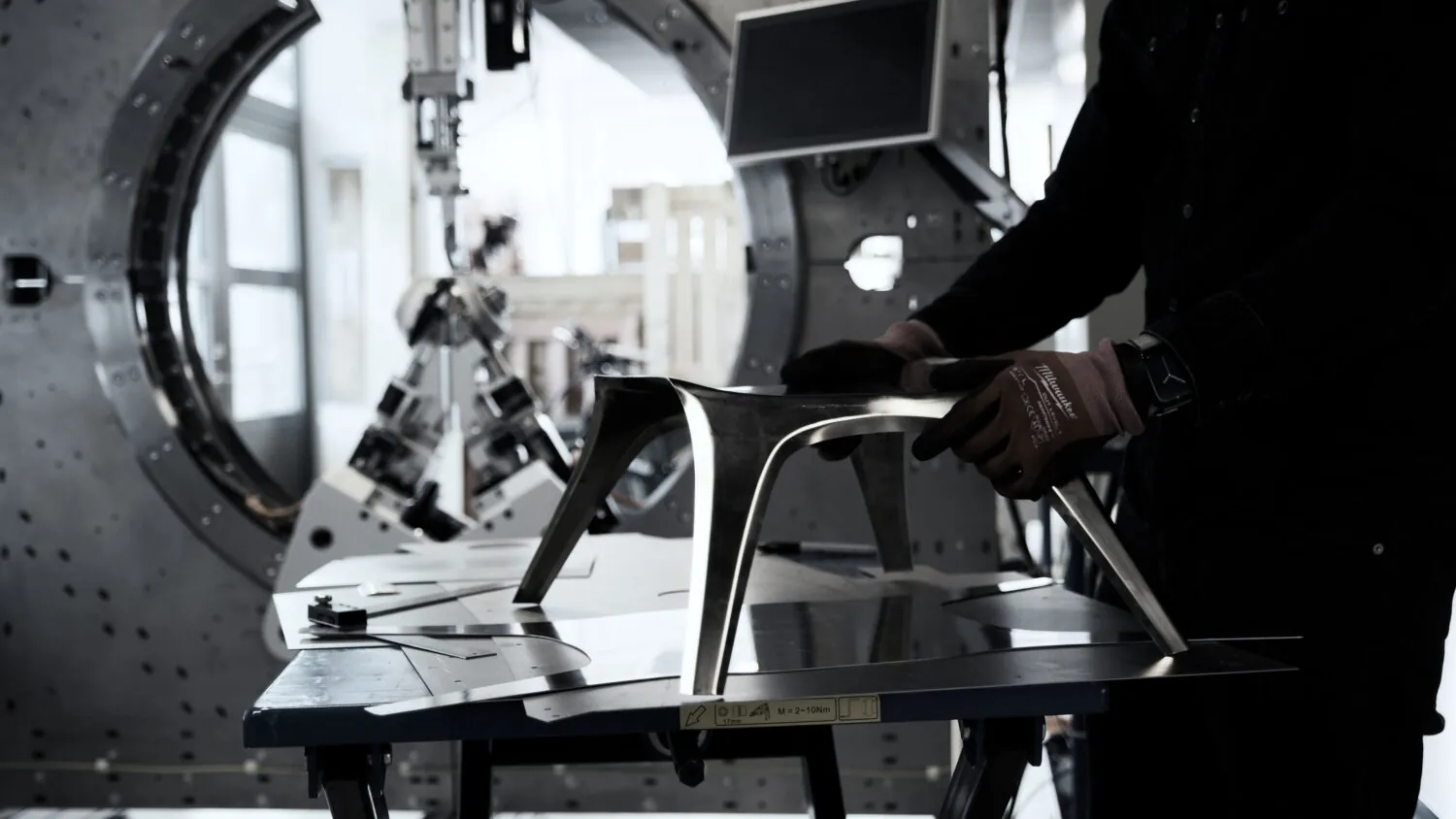
In an era where industries are under increasing pressure to reduce waste, embrace sustainable practices, and optimize production efficiency, STILFOLD has emerged as an innovator in advanced manufacturing.
Headquartered in Sweden, STILFOLD has developed a cutting-edge technique known as “industrial origami”—a process that involves folding flat sheet metal along curved lines using robotic precision. This method challenges traditional manufacturing by minimizing waste, reducing material usage, and delivering high-performance structures with superior strength-to-weight ratios.
Unlike conventional fabrication methods that often involve cutting, welding, and assembling multiple components, STILFOLD’s technique uses intelligent folding to create robust and intricate shapes from single pieces of material. It’s a vision for a cleaner, leaner, and smarter approach to manufacturing, one that aligns both with environmental requirements and the demands of high-performance industries such as automotive, aerospace, and many more.
To realize the full potential of this innovative process, STILFOLD needed a way to bring repetition, precision, and scalability to its curve-folding technology. The solution came in the form of simulation, and in collaboration with EDRMedeso, the company has now embedded simulation at the heart of its development strategy.
The broader manufacturing landscape is experiencing rapid transformation. Rising material costs, growing energy prices, regulatory demands, and the push for lightweight design are placing extraordinary strain on businesses across sectors. Manufacturers must find ways to reduce carbon footprints while maintaining, or even improving, structural performance and operational efficiency.
STILFOLD’s “industrial origami” methodology directly responds to these challenges. Its ability to transform flat sheet metal into complex forms using folding – without the need for excessive cutting or welding – offers a cleaner and more efficient path forward.
However, executing this technique at scale presents its own challenges. The process is sensitive to the physical properties of materials used and must be performed with accuracy. Any inconsistency can lead to deformation, compromised integrity, or inefficiencies in the final product.
This is where simulation becomes critical – not simply as a support tool, but as a strategic enabler of STILFOLD’s manufacturing philosophy.
The manufacturing sector is under immense pressure to meet demands for sustainability, efficiency, and cost-effectiveness, all while grappling with:
STILFOLD’s patented curve-folding technique directly addresses these challenges by minimizing waste, lowering emissions, and integrating multiple parts into a single folded structure.
Various analyses demonstrating STILFOLD’s novel folding technology
From the outset, STILFOLD recognized that to move from prototype to industrial-scale production, it would need a way to precisely predict how materials would behave during the folding process. Traditional trial-and-error approaches would be too slow, too costly, and too inconsistent to support the company’s ambitions.
STILFOLD adopted Ansys LS-DYNA, one of the world’s most advanced explicit solvers, specifically designed to handle complex material deformations and dynamic events. Within a rapid 10-month development cycle, the team succeeded in building a simulation model capable of accurately predicting curve-folded geometries based on real-world material inputs.
This simulation model serves a dual purpose. First, it enables STILFOLD to simulate the folding process digitally, ensuring that predicted outcomes match intended designs. Second, it forms the basis for programming robotic arms and the company’s newly launched curve-folding station, STILWORKS 1, which brings automation to the heart of STILFOLD’s production process.
Simulation was chosen to:
Several advanced capabilities within LS-DYNA have proven particularly valuable. The use of explicit dynamic simulations allows for the accurate modeling of large plastic deformations that occur during roll forming. In addition, co-simulation with PyFMI facilitates the integration of real-time controllers, while PyAnsys supports efficient data extraction – an essential feature for refining machine instructions and optimizing performance.
Key tools and integrations included:
While simulation work remains part of an ongoing R&D initiative, its impact is already being felt across STILFOLD’s engineering and business operations. On the technical side, simulation has drastically improved process repetition and design precision. Engineers can now predict geometric outcomes before physical production, saving time and reducing material waste.
From a business perspective, simulation has enabled faster design iterations and accelerated time-to-market. By validating their designs digitally, STILFOLD can optimize manufacturing instructions and deliver high-quality, customized solutions to clients more quickly and efficiently. And as for the future? There is strong confidence that simulation will continue to play a transformative role across customer projects and product development.
Engineering Gains:
Business Outcomes:
STILFOLD’s approach to metal fabrication is an innovative response to the manufacturing industry’s most pressing challenges. Through the application of simulation, the company has made great progress in sustainable production. With continued use of the powerful capabilities of LS-DYNA, STILFOLD is not only advancing its own technology but also helping to shape a more efficient and environmentally responsible future for global manufacturing.