Case Study: Using Simulation to Optimize Motor Design for Commercial-Grade Lawnmowers
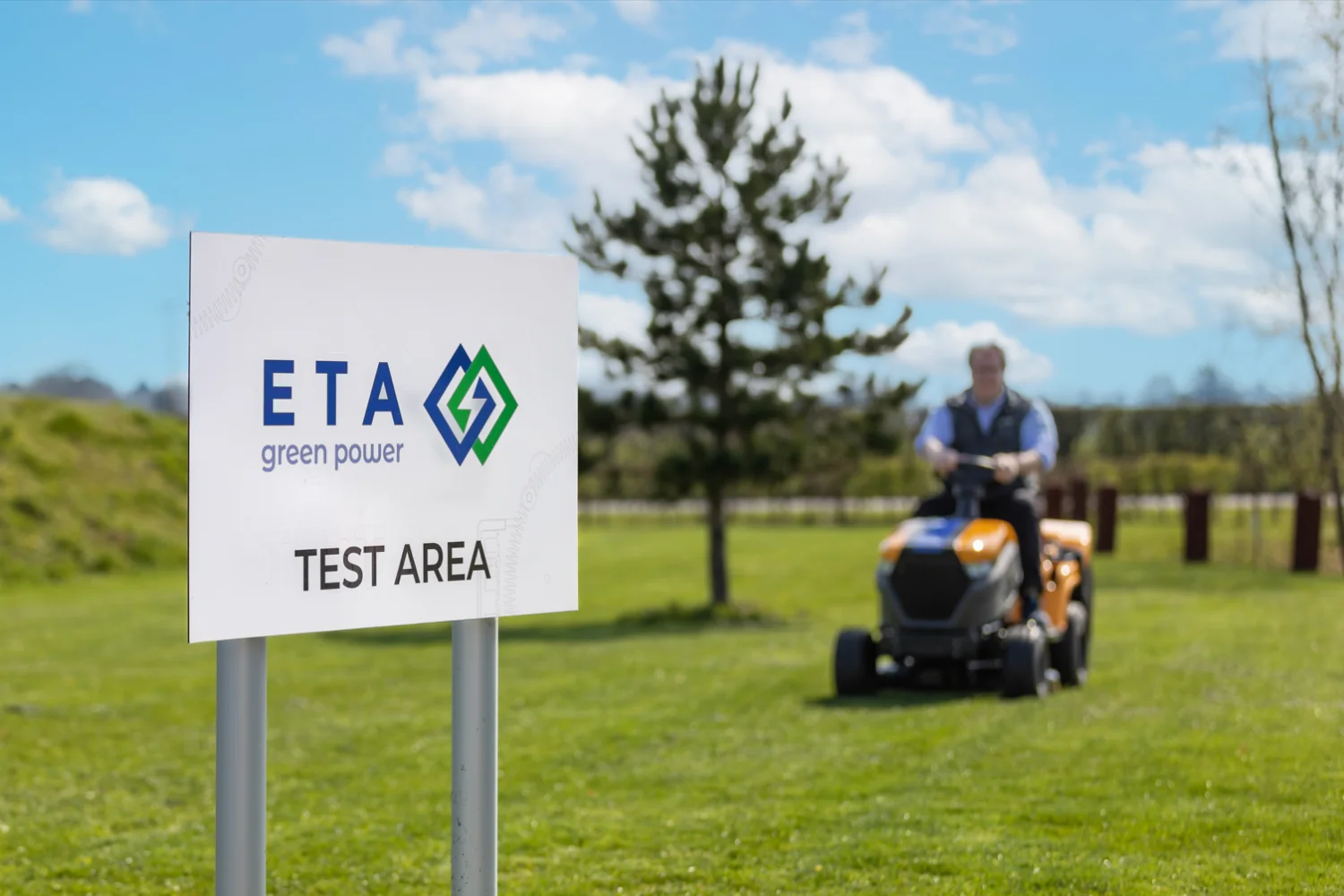
ETA Green Power is a UK-based leader in power electronics and magnetics, specializing in electrification solutions for OEMs and Tier 1 suppliers in e-Mobility, Outdoor Power Equipment, and compact construction industries. Leveraging a portfolio of over 20 patents across 40+ countries, ETA delivers patented technologies that provide up to 60% performance improvements while reducing costs, empowering its partners with a decisive competitive edge.
Through a unique licensing model, ETA enables customers to access cutting-edge innovations while maintaining full control of their product development and supply chains. Its integrated approach ensures optimal system efficiency and mitigates single points of failure, delivering reliable and robust solutions. With a strong commitment to collaboration, ETA offers ongoing support and knowledge transfer, driving successful implementation and sustained growth for its partners.
The transition from internal combustion engines (ICE) to battery-electric drives has become a critical focus for Original Equipment Manufacturers (OEMs) across various industries. This shift is driven by tightening emission regulations and growing customer demand for cleaner, more sustainable technologies. However, the journey to electrification presents significant challenges, particularly for larger machines such as construction equipment, Outdoor Power Equipment (OPE), and light motorcycles or tricycles.
These machines often struggle with following:
To enable OEM’s to overcome these challenges, ETA has adopted advanced simulation tools, enabling the company to deliver high-performance electric motor solutions efficiently and confidently. Leveraging a comprehensive suite of Ansys solutions, including Ansys Motor-CAD, Electronics Enterprise, Ansys HPC, Ansys Mechanical, and Ansys CFD, ETA ensures that every aspect of solution performance is rigorously validated. Simulation provides:
A critical aspect of ETA’s business involves designing and developing motors for commercial-grade applications, including lawnmowers. One of the key risks these products face is the impact of sudden stop events, such as when a rotating blade strikes debris during operation.
To address this, ETA collaborated with EDRMedeso to analyze the effect of a shock load caused by such a collision. The goal was to assess the induced loads and identify potential structural integrity issues, using a simulation approach applicable across ETA’s solutions.
1. Scenario Setup:
2. Boundary Conditions:
3. Tool Used:
4. Key Observations:
1. Risk Mitigation
2. Time and Cost Efficiency
3. Enhanced Design Performance
4. Industry-Specific Insights
By collaborating with EDRMedeso and leveraging tools like Ansys LS-Dyna, ETA successfully identified and addressed potential risks, enhancing the performance and durability of its motor solutions.
Simulation has become an integral part of ETA’s development process, enabling the company to remain a leader in the electrification of machinery and vehicles. By combining industry expertise with cutting-edge technology, ETA continues to empower its clients with solutions that not only meet but exceed the evolving demands of the market.