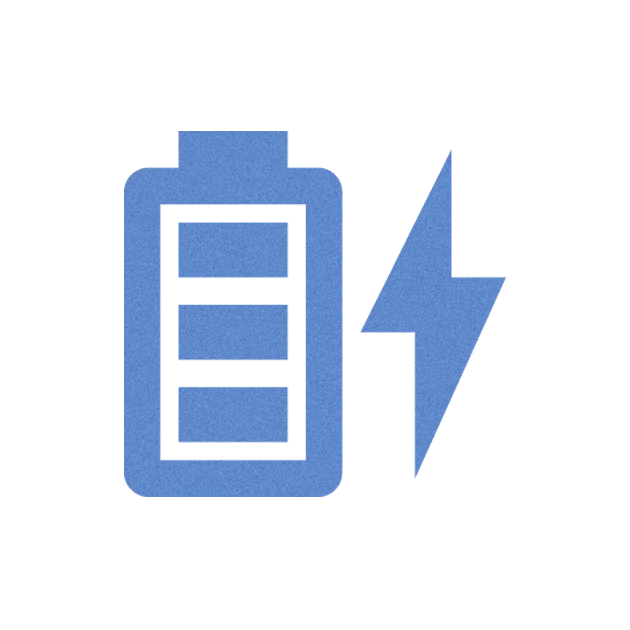
Battery Simulation is a powerful solution that enables you to design and optimize battery systems using simulation technology. With Ansys Battery Simulation, you can achieve better performance, longer battery life, and reduced costs while accelerating the product development process.
Accurate Behavior Modeling with Battery Simulation
Battery Simulation offers a comprehensive simulation process that enables you to design, model, and simulate complex battery systems in a virtual environment. The simulation process includes battery cell modelling, pack modelling, system integration, and testing and validation.
Battery cell modelling allows you to accurately model the behaviour of different types of battery cells. Pack modelling enables you to design and optimize the battery pack layout, thermal management system, and other components. System integration enables you to integrate the battery pack with other systems such as electric motors and power electronics. Testing and validation allows you to test and validate the battery system’s performance under various operating conditions.
Benefits
Ensuring Functional Safety for BMS Designs
Developing Critical Embedded Software
Achieving a System-Level Perspective
Reduces Cost and Development Time
How We Can Help
We enable our customers to design better products, reduce risk, and accelerate time to market. At EDRMedeso we are committed to driving innovation by providing leading simulation technologies powered by knowledge transfer.
Our experienced engineers can help you design, optimize, and test battery systems. We offer consulting services to provide guidance on battery system design, modeling, and simulation. Additionally, we offer Battery System training programs to help you get the most out of the software.
Speak to an Expert
Reach out to our expert for help or advice